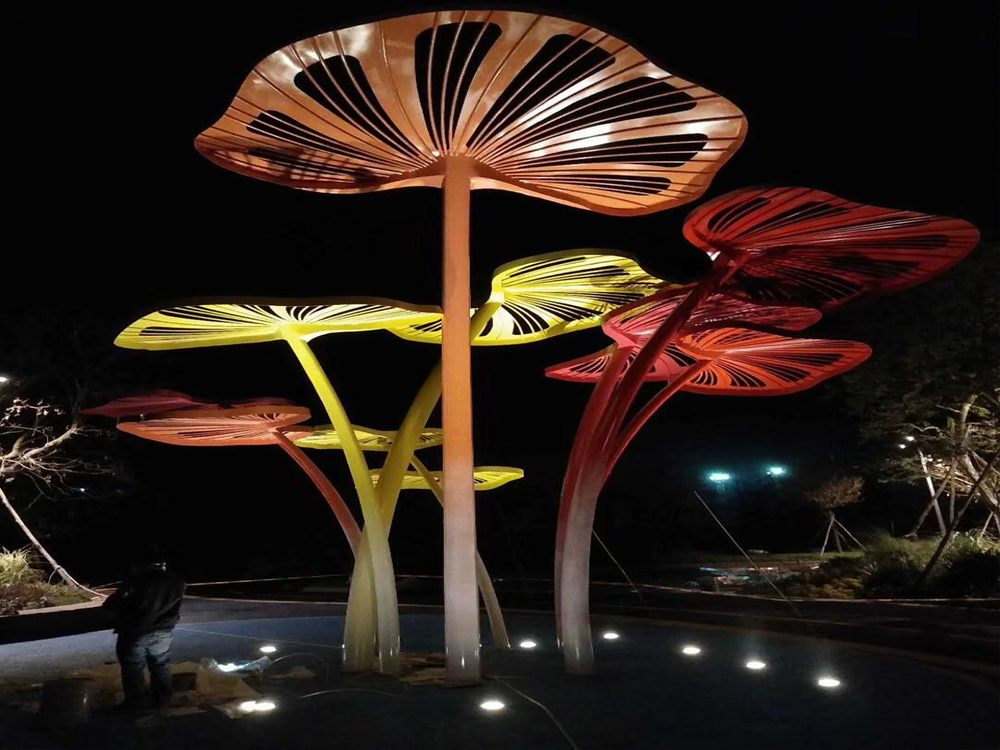
Creating porcelain sculptures with embedded lighting is a delicate fusion of artistry and engineering, presenting unique challenges that demand precision and innovation. One major hurdle is the fragility of porcelain, which complicates the integration of electrical components without compromising structural integrity. Artists must carefully plan hollow cavities or channels during the sculpting phase to accommodate wiring while avoiding cracks during firing.
Thermal management is another critical issue, as traditional kiln firing can damage sensitive lighting elements like LEDs. Many creators resort to post-firing installation, requiring meticulous measurement to ensure perfect component fit. The translucent quality of porcelain also poses lighting design challenges – too much diffusion can dull the effect, while uneven thickness creates hot spots.
Electrical safety presents further complications, especially for pieces intended as functional lighting. Waterproofing connections and ensuring proper insulation becomes crucial when combining conductive materials with porous ceramics. Lastly, the weight distribution of both porcelain and lighting components requires thoughtful engineering to prevent top-heavy sculptures from becoming unstable.
Successful artists overcome these obstacles through innovative techniques like 3D-printed porcelain molds, low-temperature firing clay bodies, and modular assembly approaches that allow for lighting system maintenance. The result are breathtaking illuminated sculptures that push the boundaries of both ceramic art and lighting design.