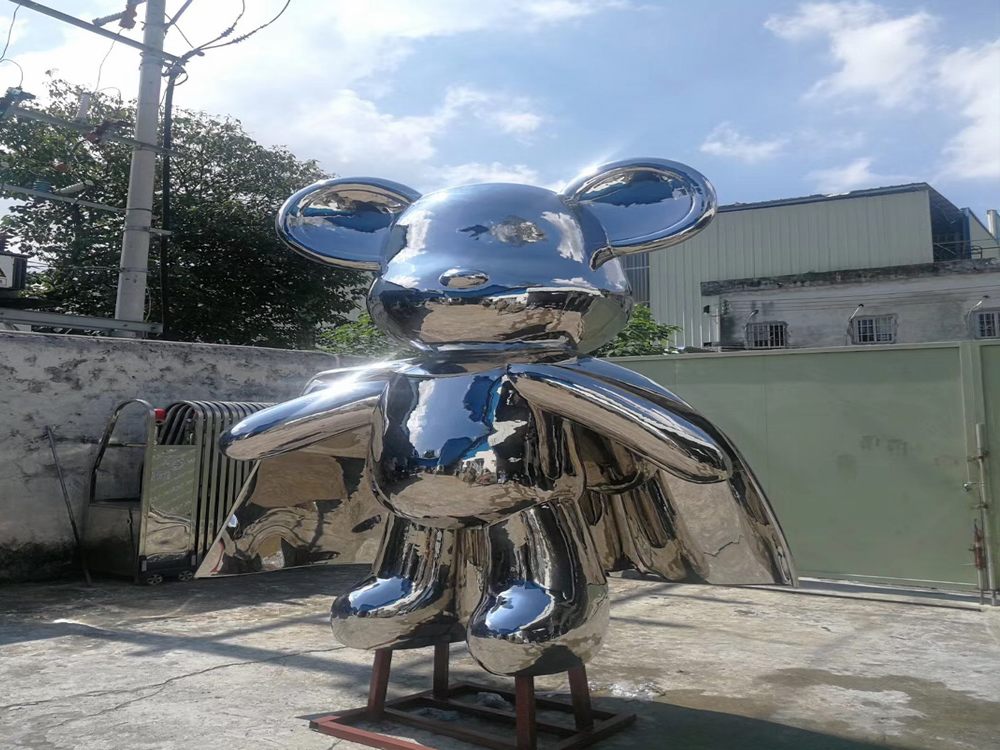
The advent of 3D printing technology has profoundly reshaped the creation of porcelain sculptures, merging traditional craftsmanship with cutting-edge innovation. Unlike conventional hand-molding techniques, 3D printing allows artists to achieve unprecedented precision in complex geometries—think delicate latticework or interlocking patterns—that were once impossible or prohibitively time-consuming.
Designers now leverage digital modeling software to experiment freely, iterating prototypes in hours rather than weeks. This accelerates creative exploration while reducing material waste, as virtual adjustments replace physical trial-and-error. Small-batch production benefits particularly, with printers replicating intricate designs consistently—a boon for limited-edition art pieces.
For manufacturers, 3D printing slashes lead times by automating mold creation. Traditional plaster mold-making, requiring skilled labor and multiple curing stages, gives way to direct printing of ceramic or resin molds ready for slip-casting. Hybrid approaches are emerging too: artists 3D-print structural armatures for hand-applied porcelain, blending digital efficiency with tactile artistry.
Customization reaches new heights as well. Collectors can commission personalized sculptures scaled to millimeter specifications, while restoration projects use 3D scanning to recreate fragile antique details. However, challenges persist—glaze compatibility with printed layers and the need for post-processing remind us that technology complements, rather than replaces, the potter’s expertise.
Ultimately, 3D printing democratizes porcelain art, empowering both established studios and independent makers to push boundaries while honoring ceramic traditions in the digital age.