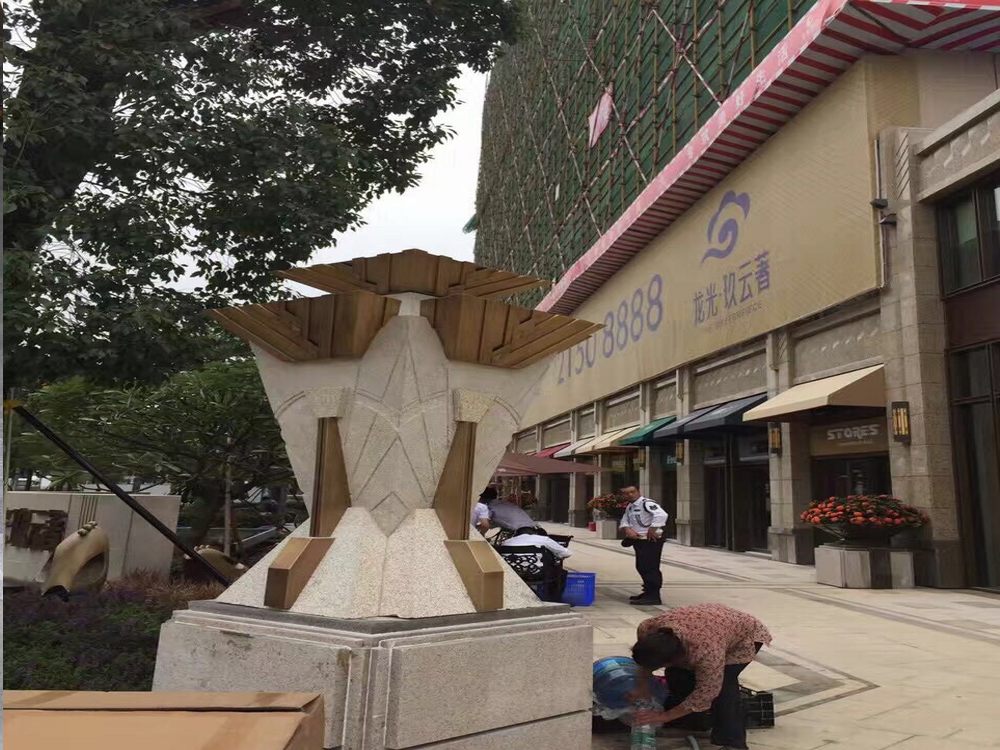
Porcelain sculptures, renowned for their delicate beauty, often face challenges in transportation due to their fragility. Contemporary artists have ingeniously adopted modular and assemblable designs to overcome this hurdle while preserving artistic vision.
The modular approach involves creating sculptures in interlocking sections that can be safely packed and reassembled. Artists carefully design each component with precision-engineered joints - sometimes using threaded connectors, magnetic fittings, or tongue-and-groove systems specifically adapted for ceramic materials. This method allows large-scale works to be transported as multiple smaller, more manageable pieces.
Assemblable designs take this concept further by incorporating elements that only achieve their final form when combined. Some artists create puzzle-like sculptures where each fragment contributes to the overall composition, while others design pieces that can be arranged in multiple configurations, adding an interactive dimension to the artwork.
Advanced techniques include:
1. 3D-printed porcelain connectors that ensure perfect fit
2. Hidden joining systems that maintain visual continuity
3. Custom foam packaging shaped to each modular component
4. Numbered or color-coded assembly guides
These innovations not only solve practical transport issues but often enhance the artistic concept, with the assembly process becoming part of the artwork's narrative. Collectors appreciate how these designs reduce insurance costs and shipping risks while maintaining the sculpture's value and integrity.
The trend reflects a broader movement in ceramic art towards functional creativity, where practical solutions become integral to artistic expression rather than compromises to it. As shipping costs rise and international exhibitions increase, these transport-friendly designs are revolutionizing how delicate porcelain art circulates in the global market.