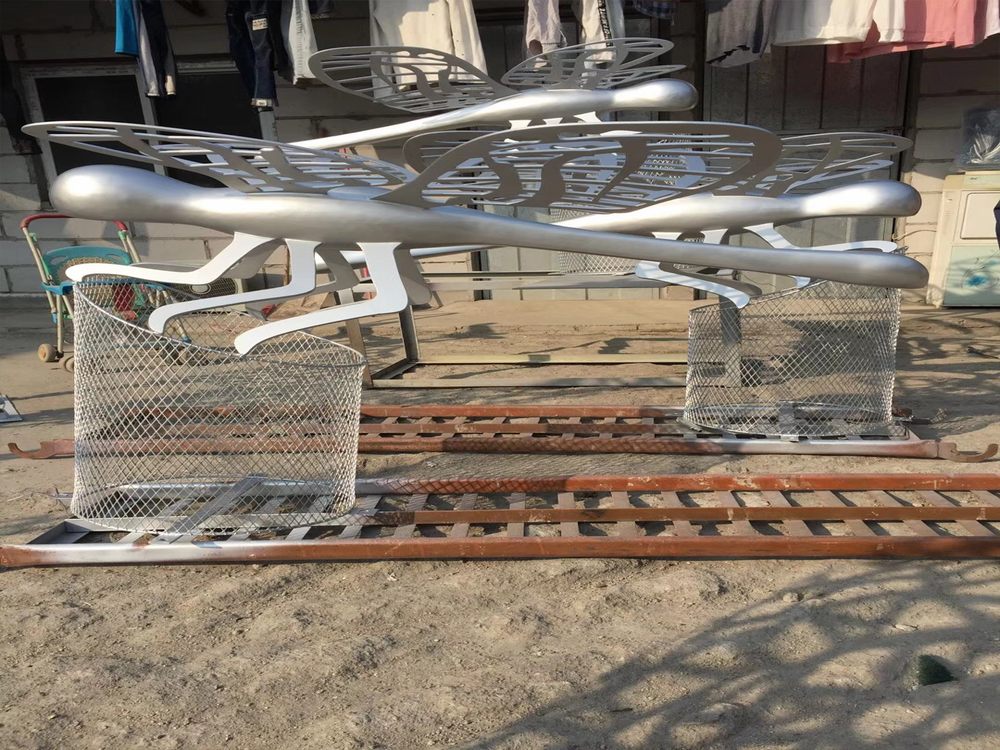
Creating hand-painted porcelain sculptures with consistent colors is a meticulous process that requires both artistic skill and technical precision. Artisans rely on several key methods to ensure uniformity across each piece.
First, they use high-quality ceramic pigments specifically formulated for porcelain. These pigments are carefully measured and mixed to create exact shades, often following traditional recipes passed down through generations. The consistency of the pigment mixture is crucial, as even slight variations can alter the final color after firing.
Second, artisans employ standardized firing techniques. Porcelain must be fired at precise temperatures to achieve the desired color intensity and durability. Experienced craftsmen monitor kiln conditions closely, as over- or under-firing can lead to discoloration. Many workshops maintain detailed firing logs to replicate successful results.
Third, master painters often work on multiple pieces simultaneously, applying colors in the same order and with identical brushstrokes. This systematic approach minimizes variations between individual sculptures. Some artisans use stencils or tracing methods for complex designs to ensure pattern consistency.
Finally, rigorous quality control plays a vital role. Each piece undergoes multiple inspections during production, with adjustments made to maintain color harmony. This attention to detail transforms porcelain from mere craft into enduring art.
The result is a collection of sculptures where every hue remains true to the artist's vision, preserving both aesthetic beauty and cultural heritage in each brushstroke.