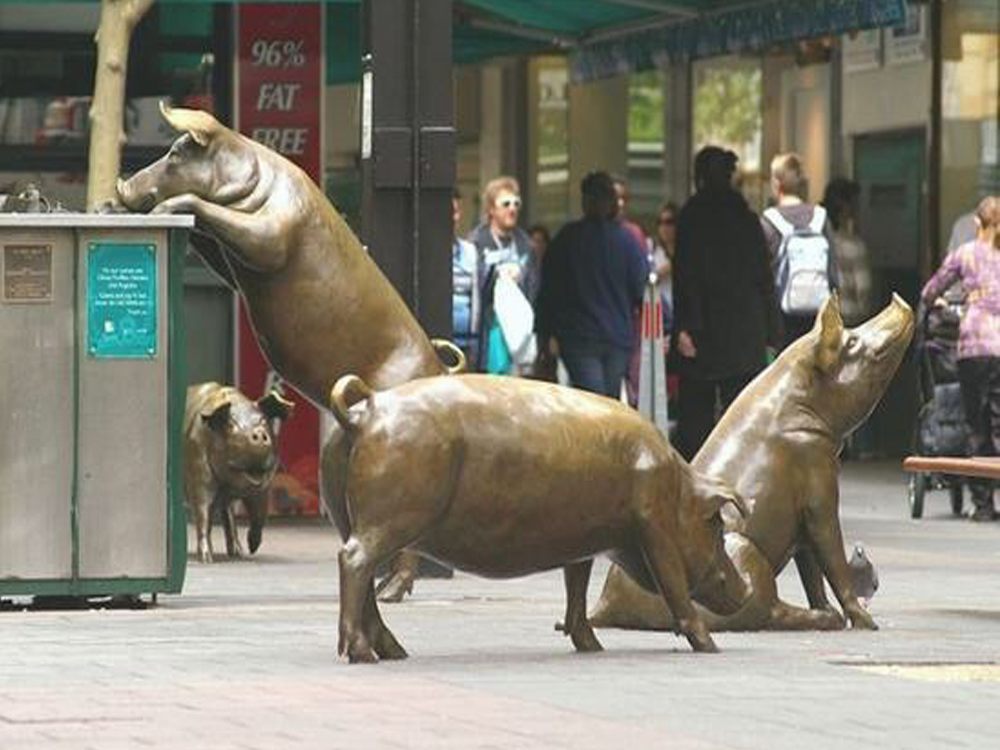
The advent of modern 3D printing technologies has significantly disrupted traditional methods of creating porcelain sculptures, introducing unprecedented precision, efficiency, and creative possibilities. Unlike conventional techniques—which rely on hand-molding, wheel-throwing, and kiln-firing—3D printing allows artists to produce intricate designs with minimal material waste and faster turnaround times.
One of the most notable impacts is the democratization of porcelain art. Traditional methods require years of mastery, whereas 3D printing enables even novice creators to experiment with complex geometries and personalized designs. Additionally, digital tools facilitate the replication of sculptures with exact consistency, a challenge in manual craftsmanship.
However, purists argue that 3D-printed porcelain lacks the tactile authenticity and organic imperfections of handcrafted pieces. Despite this, hybrid approaches—combining 3D-printed bases with hand-finished details—are gaining traction, bridging the gap between innovation and tradition.
As the technology evolves, 3D printing is poised to redefine porcelain sculpture, not as a replacement for tradition, but as a complementary force expanding artistic horizons.