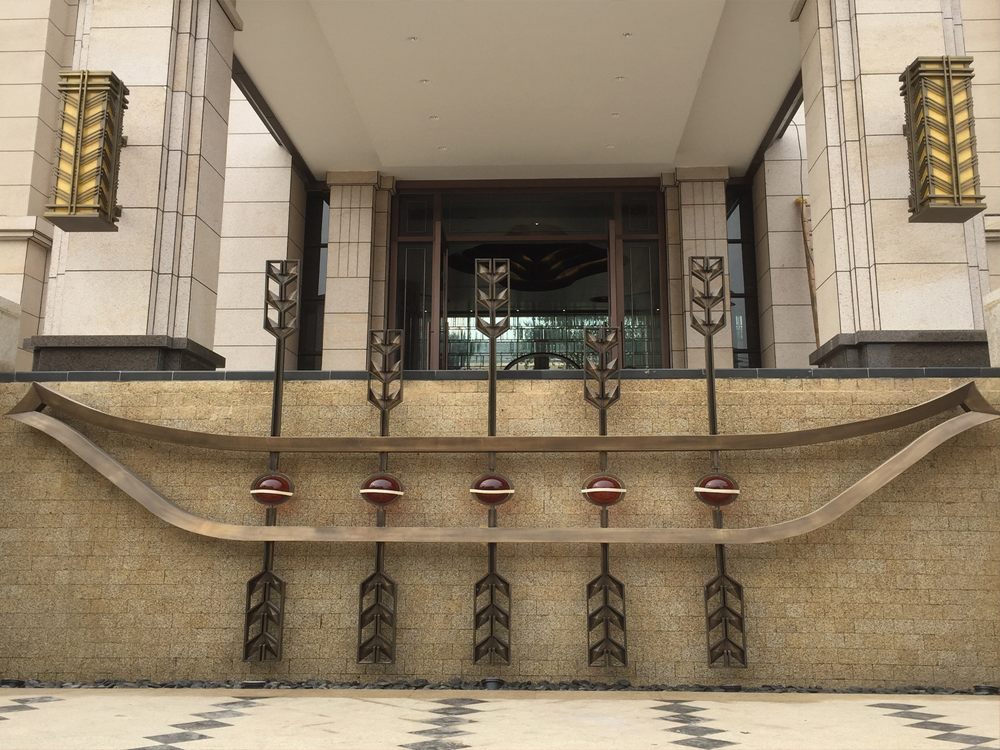
Creating porcelain sculptures with modular or interchangeable components presents unique challenges that test the limits of ceramic artistry. The fragility of porcelain demands meticulous precision in design and execution, as even minor imperfections can compromise the integrity of interlocking parts. Achieving consistent shrinkage rates during firing is critical, as uneven contraction may render components incompatible. Glazing introduces further complexity, as variations in thickness can alter fit tolerances. Structural stability becomes a balancing act, requiring innovative engineering to maintain aesthetic appeal while ensuring durability. Artists must also consider the long-term wear of repeated assembly and disassembly, which can lead to micro-fractures over time. These challenges push creators to blend traditional craftsmanship with modern design thinking, resulting in works that marry delicate beauty with functional ingenuity.