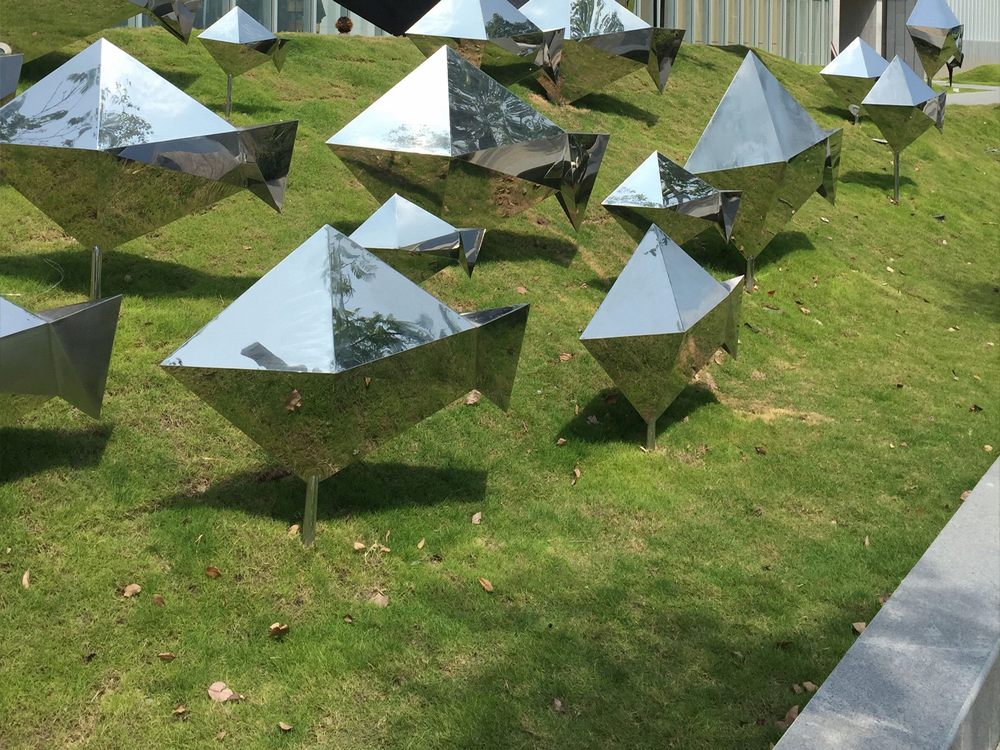
The delicate translucency of thin porcelain sculpture components is achieved through a combination of meticulous material selection, precise craftsmanship, and specialized firing techniques. Artisans begin by using high-quality kaolin clay with exceptional purity, which allows light to penetrate the thin walls of the sculpture. The clay is carefully wedged to remove air bubbles and rolled or pressed to an even thickness, typically less than 2mm.
Master potters employ unique throwing and carving techniques to create paper-thin sections while maintaining structural integrity. The real magic happens during the firing process - a carefully controlled dual firing method where the initial bisque firing stabilizes the form, followed by a high-temperature glaze firing at 1280-1400°C that vitrifies the clay into translucent porcelain.
Some artisans enhance the effect by applying multiple thin layers of specially formulated translucent glazes, each fired separately. Others use a technique called "light carving," where they strategically thin certain areas from the back to create graduated transparency. The final result is a breathtaking interplay of light and material, where porcelain appears to glow from within, showcasing the pinnacle of ceramic artistry.