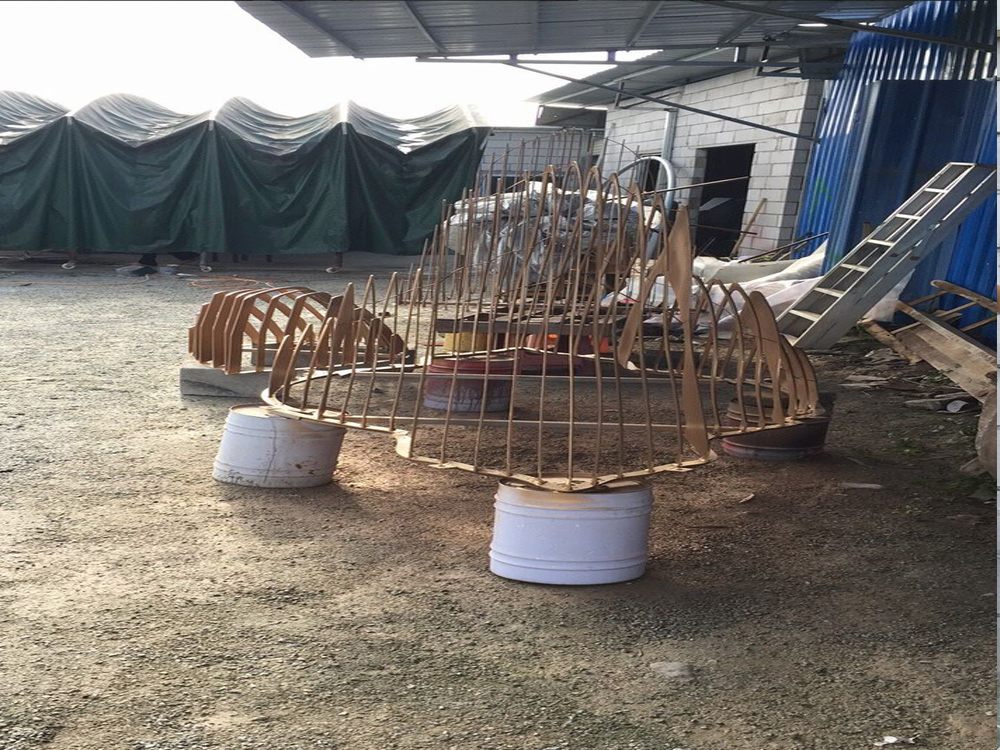
Scaling up production for high-demand porcelain sculpture designs presents a unique set of challenges that blend artistry with industrial constraints. One major hurdle is the delicate nature of porcelain itself—its fragility demands meticulous handling during mass production, often leading to higher breakage rates. The intricate detailing required in premium sculptures also complicates automation, forcing manufacturers to rely heavily on skilled artisans whose expertise is both scarce and costly.
Material consistency poses another obstacle, as even minor variations in clay composition or kiln temperatures can dramatically alter the final product's quality. Supply chain bottlenecks for specialized glazes and pigments further exacerbate delays, particularly when global demand surges unexpectedly.
Additionally, the lengthy firing process—often requiring multiple kiln cycles—creates production bottlenecks that are difficult to overcome without compromising artistic integrity. Many studios face the dilemma of maintaining handcrafted authenticity while attempting to meet commercial quantities, as collectors increasingly value the "artist's touch" that distinguishes limited editions.
Environmental regulations add another layer of complexity, with strict controls on kiln emissions and waste disposal limiting expansion options for traditional workshops. These multifaceted challenges require innovative solutions that balance scalability with the uncompromising quality standards demanded by discerning collectors worldwide.