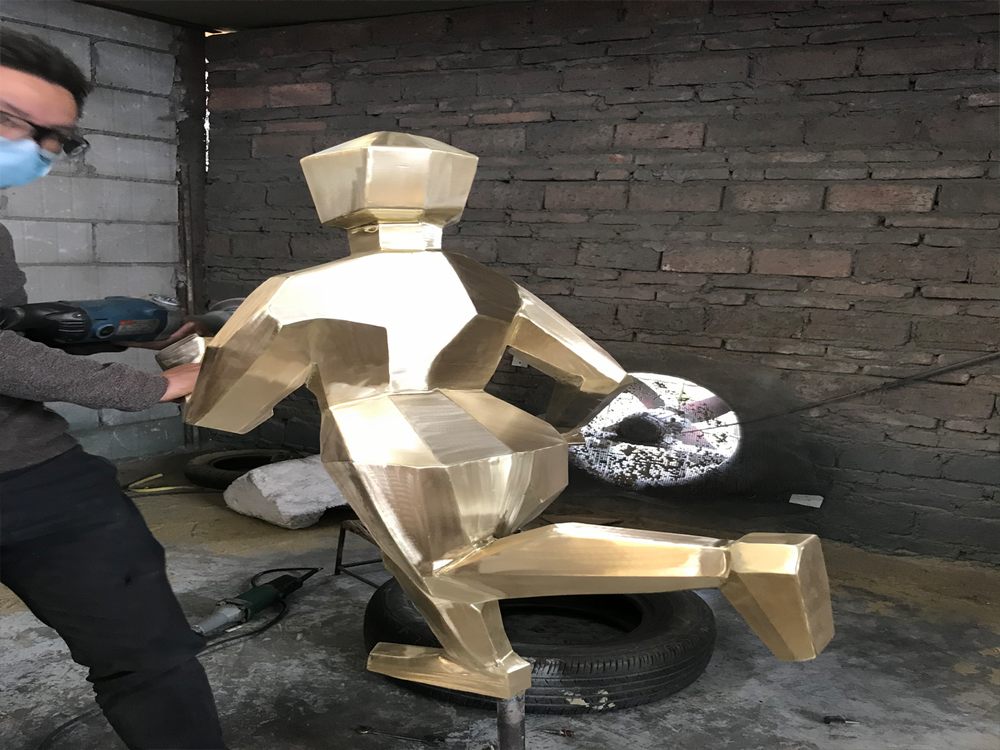
Creating porcelain sculptures with intricate, perforated surfaces is a testament to an artist’s patience, skill, and innovation. The delicate nature of porcelain demands meticulous handling, especially when crafting fine perforations that risk cracking or collapsing during the drying and firing stages.
Artists begin by selecting high-quality porcelain clay, prized for its fine particle size and plasticity, which allows for precise detailing. To achieve perforated designs, they employ techniques like piercing, carving, or using specialized tools such as fine needles or laser-cut templates. Some even layer thin sheets of clay, carving patterns before assembling the pieces.
Drying is a critical phase—artists often work in controlled humidity environments to prevent warping. Kiln firing requires precise temperature management to avoid thermal shock, with some opting for multiple low-temperature firings to preserve structural integrity.
Innovations like 3D-printed molds or slip-casting with perforated templates have expanded possibilities, blending traditional craftsmanship with modern technology. The result is breathtaking sculptures that balance fragility and strength, showcasing the artist’s mastery over this demanding medium.