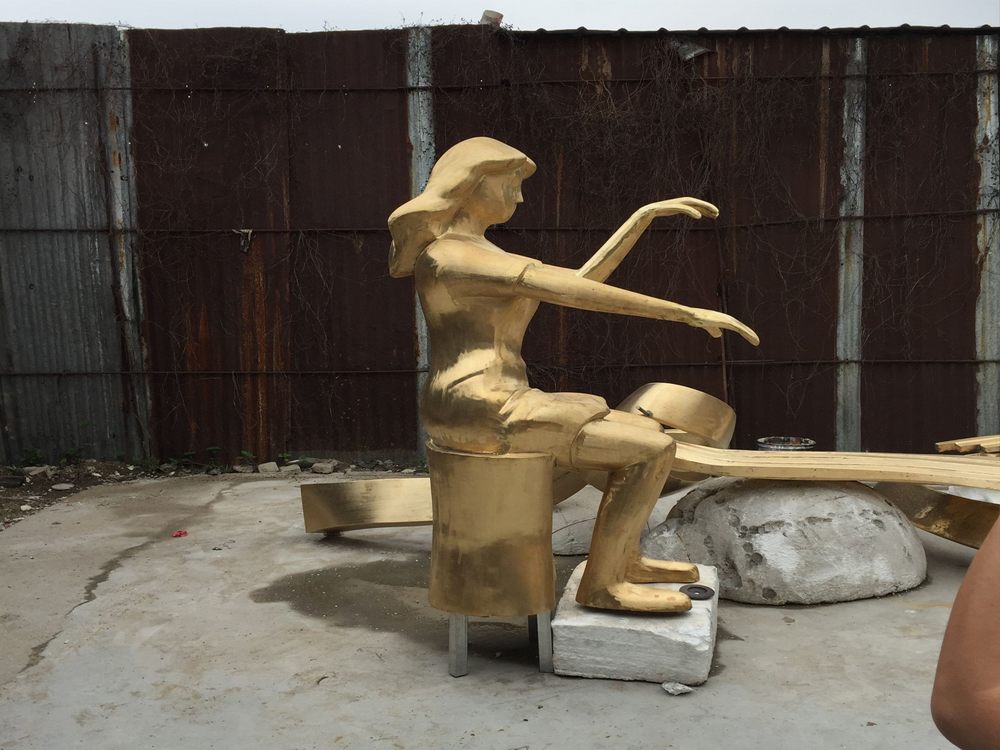
Achieving uniform color batches in porcelain glaze production is a complex process fraught with challenges. One major issue is the variability of raw materials, as natural minerals and pigments often differ in composition, leading to subtle shade discrepancies. Firing conditions also play a critical role – even minor fluctuations in kiln temperature, atmosphere, or cooling rates can dramatically alter final glaze colors.
The chemical interactions between glaze components further complicate consistency. Certain colorants may react unpredictably when combined, while variations in glaze thickness application can result in noticeable color differences. Additionally, the particle size distribution of raw materials affects how light interacts with the finished surface, influencing perceived color.
Manufacturers must also contend with batch-to-bag differences in commercial stains and the challenge of accurately reproducing colors from small test batches to full production runs. Even when using identical formulas, differences in mixing equipment or application methods can introduce variations.
To address these challenges, producers implement rigorous quality control measures, including standardized testing protocols, precise raw material sourcing, and advanced kiln monitoring systems. Many now employ digital color matching technology to detect subtle variations before firing. Despite these efforts, maintaining perfect color consistency remains one of the most demanding aspects of high-quality porcelain production.