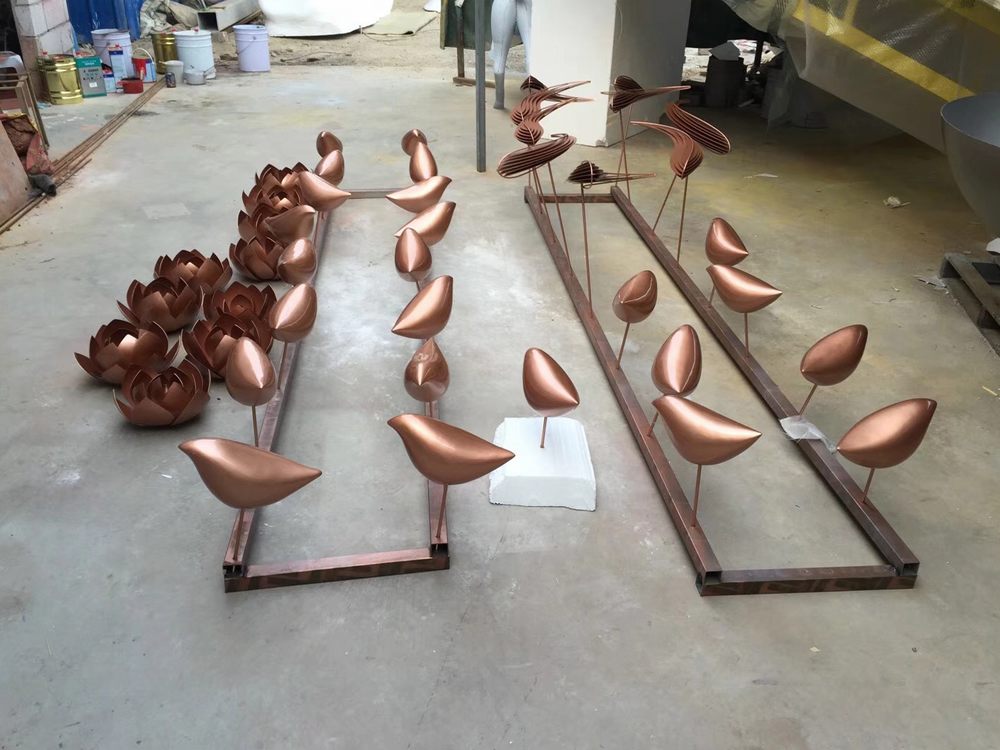
Creating porcelain sculptures with integrated kinetic or mechanical parts presents a unique set of challenges that test the limits of both artistry and engineering. Porcelain, known for its delicate beauty, is inherently fragile, making it difficult to incorporate moving components without compromising structural integrity. The material's brittleness requires precise engineering to avoid cracks or breaks during movement.
Another challenge lies in the design process. Artists must balance aesthetic appeal with functional mechanics, ensuring that the kinetic elements enhance rather than detract from the sculpture's visual harmony. The integration of gears, hinges, or motors demands meticulous planning to avoid disrupting the porcelain's elegant form.
Additionally, firing porcelain at high temperatures can warp or damage mechanical parts, necessitating post-firing assembly—a delicate and time-consuming process. Moisture sensitivity further complicates long-term durability, as repeated movement may weaken joints or cause wear.
Despite these hurdles, the fusion of porcelain and kinetic art offers breathtaking results, pushing the boundaries of traditional ceramic sculpture. Innovators in this field continue to experiment with hybrid techniques, blending ancient craftsmanship with modern mechanics to create mesmerizing, dynamic artworks.