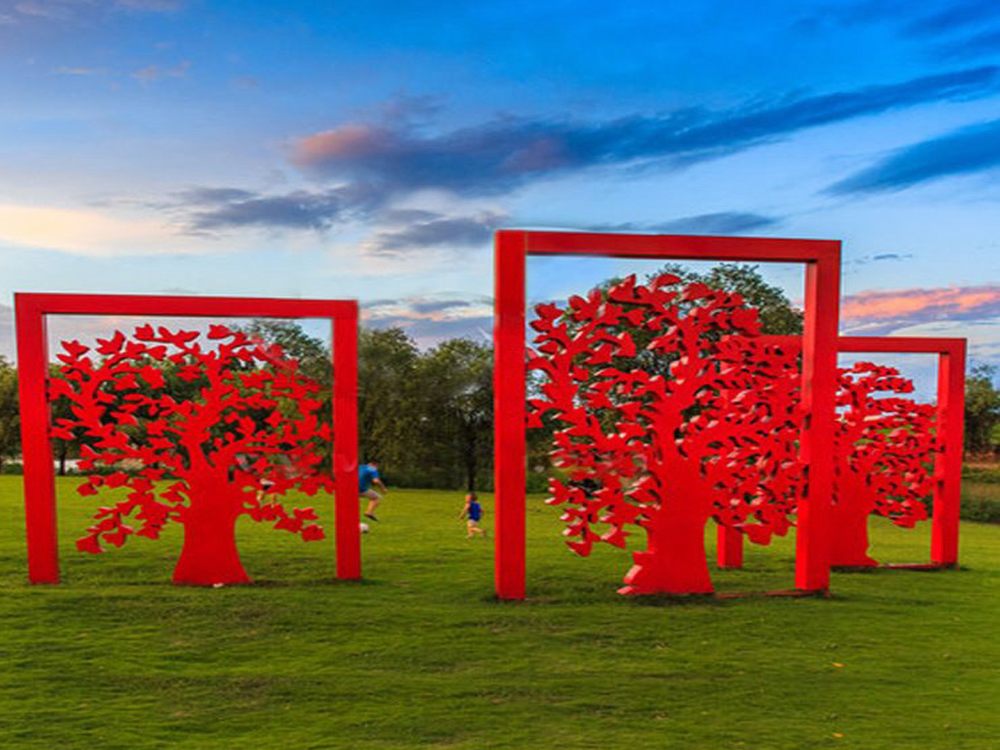
Bronze casting is a delicate art form where even minor flaws like shrinkage cavities can ruin a masterpiece. Artists employ several techniques to prevent these defects, ensuring smooth, durable sculptures.
1. Optimal Pouring Temperature: Maintaining the correct molten bronze temperature is critical. Too hot, and the metal contracts excessively; too cool, and it may not fill the mold properly. Artists use pyrometers to monitor and adjust temperatures precisely.
2. Strategic Riser Placement: Risers, or feed heads, act as reservoirs of molten metal to compensate for shrinkage as the bronze cools. Placing them near thicker sections ensures continuous metal flow, reducing cavity formation.
3. Controlled Cooling Rates: Gradual cooling minimizes uneven contraction. Artists often use insulating materials or controlled furnace environments to regulate the cooling process.
4. Proper Mold Design: A well-designed mold with tapered walls and adequate venting allows even metal distribution and reduces trapped air, which can exacerbate shrinkage.
5. Alloy Adjustments: Some artists modify bronze alloys with additives like silicon or phosphorus to improve fluidity and reduce shrinkage tendencies.
By mastering these methods, artists achieve flawless bronze castings, preserving intricate details and structural integrity in their work.