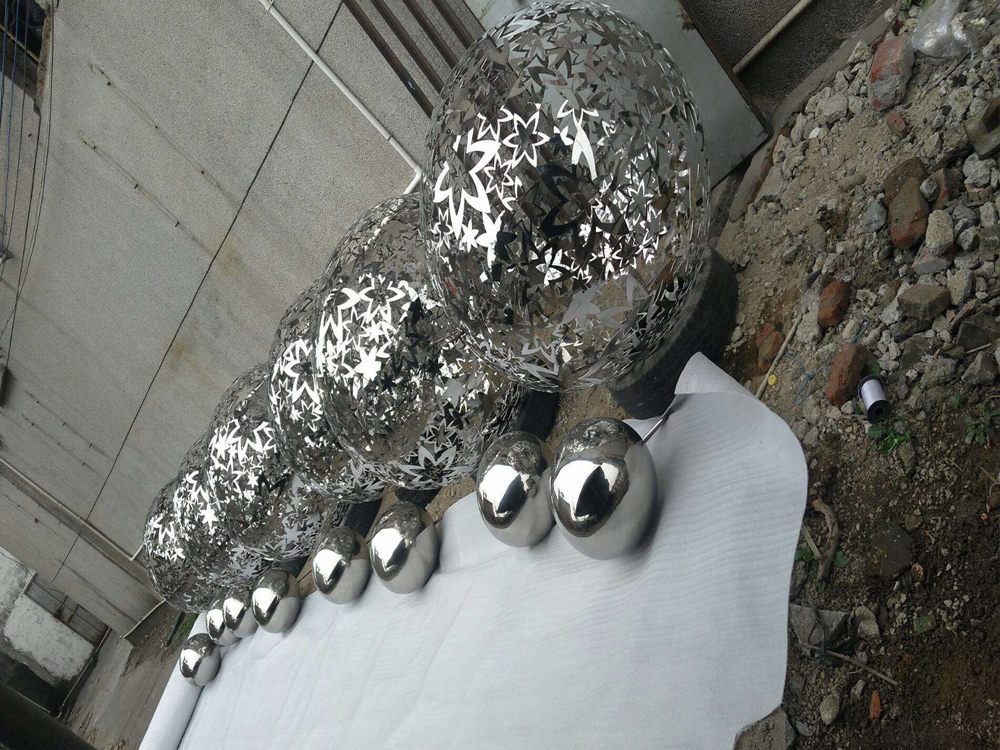
Creating flawless porcelain sculptures requires meticulous attention to glaze fit—the harmony between clay body and glaze during firing. Artists and manufacturers employ multiple strategies to address this challenge on complex shapes.
1. Material Science: Custom-blended clay and glaze formulas are developed to match thermal expansion rates. High-quality kaolin with precise silica-alumina ratios minimizes cracking.
2. Layered Application: Multiple thin glaze coats are applied via spraying or brushing, allowing even coverage on undercuts and fine details. Some artists use wax resist techniques to control glaze flow.
3. Kiln Mastery: Slow bisque firing (under 1000°C) stabilizes the sculpture before glazing. Final firings use computer-controlled ramping, often with extended soaking periods at critical temperatures to ensure glaze maturity.
4. Test Tiles & Prototyping: Miniature versions of complex sections are glazed and fired to predict behavior. Digital 3D modeling now aids in identifying potential stress points before production.
5. Innovative Formulation: Contemporary artists incorporate nano-materials and glass frits to enhance glaze elasticity. Some manufacturers add zirconium or tin oxide to improve opacity and fit on challenging geometries.
The intersection of traditional craftsmanship and modern technology continues to push boundaries in ceramic art, turning glaze fit challenges into opportunities for artistic innovation.