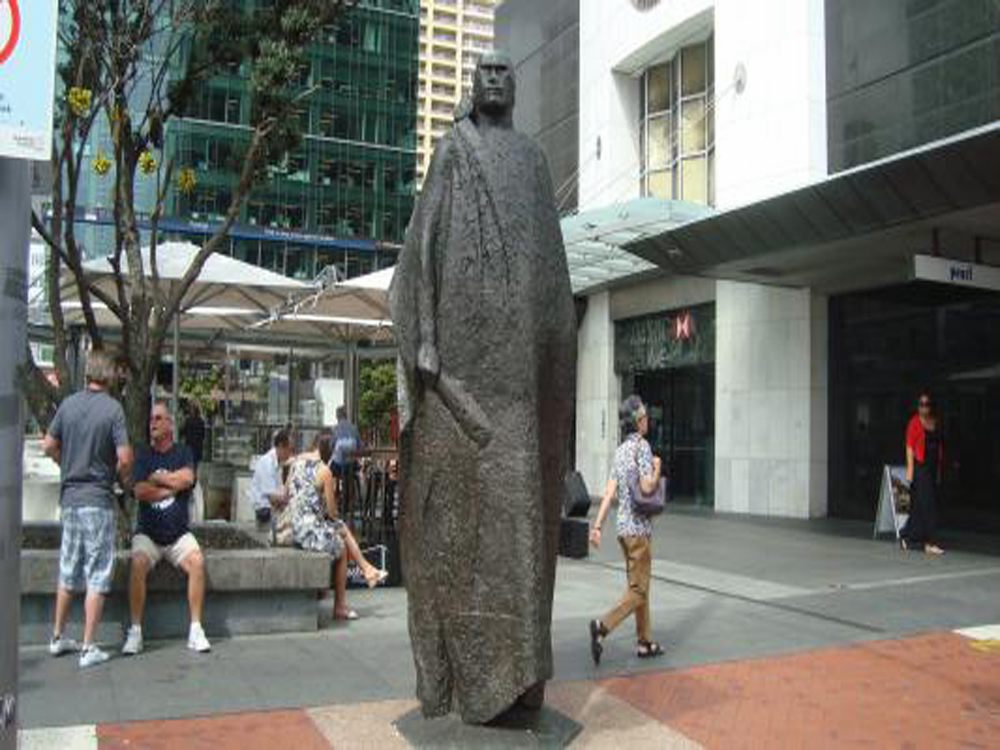
Porcelain sculptures are delicate artworks that require precise firing conditions to maintain their intended shape. However, warping or deformation during firing is a frequent challenge for ceramic artists. The most common causes include uneven heating or cooling rates in the kiln, which create stress within the clay body. Rapid temperature changes can cause differential shrinkage, leading to distortion.
Another significant factor is improper clay composition or preparation. Impurities, uneven moisture distribution, or inadequate wedging can result in weak spots that deform under heat. The thickness of the sculpture also plays a role—thicker sections dry and fire slower than thin areas, causing uneven contraction.
Kiln placement matters too. Sculptures placed too close to kiln elements may experience localized overheating, while poor airflow can create hot spots. Additionally, insufficient support structures or improper use of kiln furniture may allow pieces to sag under their own weight during the firing process.
Understanding these causes helps artists prevent defects and achieve perfectly fired porcelain sculptures every time.