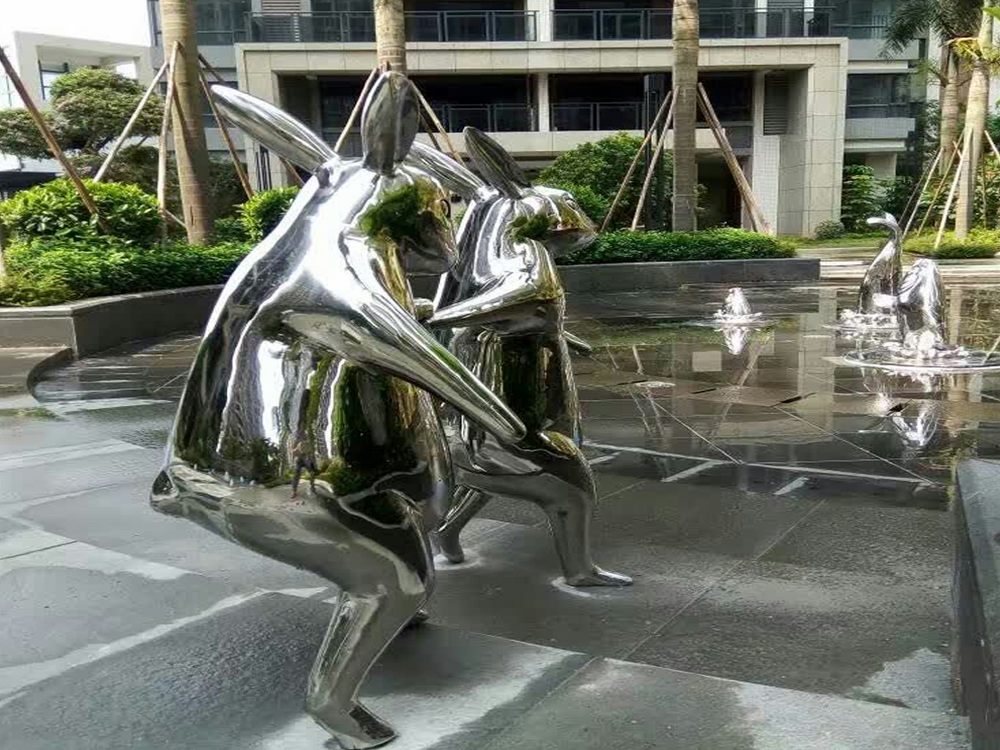
The preservation of interactive porcelain sculptures presents unique challenges that test the limits of modern conservation techniques. Unlike static artworks, these delicate pieces combine artistic vision with functional mechanics, making their long-term survival particularly complex.
Material fragility stands as the foremost obstacle. Porcelain's brittle nature makes movable joints, rotating parts, and touch-sensitive components vulnerable to stress fractures. Even gentle repeated interaction can cause microfractures that accumulate over decades. Temperature fluctuations exacerbate this issue, as porcelain expands and contracts differently than metal or wood components often used in interactive mechanisms.
Environmental factors pose another major threat. Humidity variations cause glaze deterioration, while airborne pollutants chemically interact with both porcelain and its decorative elements. Light exposure fades pigments and weakens adhesives used in repairs. Museums face the dilemma of balancing public engagement with controlled display conditions – a challenge amplified for pieces designed to be handled.
The evolution of interactive technology creates obsolescence challenges. Early kinetic porcelain sculptures relied on mechanical systems that may no longer function or lack replacement parts. Contemporary pieces incorporating electronics face rapid technological obsolescence, with circuitry and software becoming outdated within years rather than centuries.
Conservation ethics present philosophical dilemmas. Should restorers replace original interactive mechanisms with modern equivalents when originals fail? How much alteration is acceptable to maintain functionality while preserving artistic integrity? These questions lack universal answers in the conservation community.
Preventive conservation strategies have emerged as the most effective approach. Microclimate display cases with regulated humidity, specialized handling protocols, and limited interaction cycles help extend lifespan. Advanced imaging techniques now document original mechanisms before deterioration occurs, preserving at least the knowledge of how pieces were meant to function.
The field continues evolving as conservators collaborate with materials scientists and engineers. Nanotechnology coatings show promise for protecting vulnerable surfaces without altering appearance, while 3D printing enables precise replication of broken components. These innovations offer hope that future generations may still experience the tactile wonder of historic interactive porcelain masterpieces.