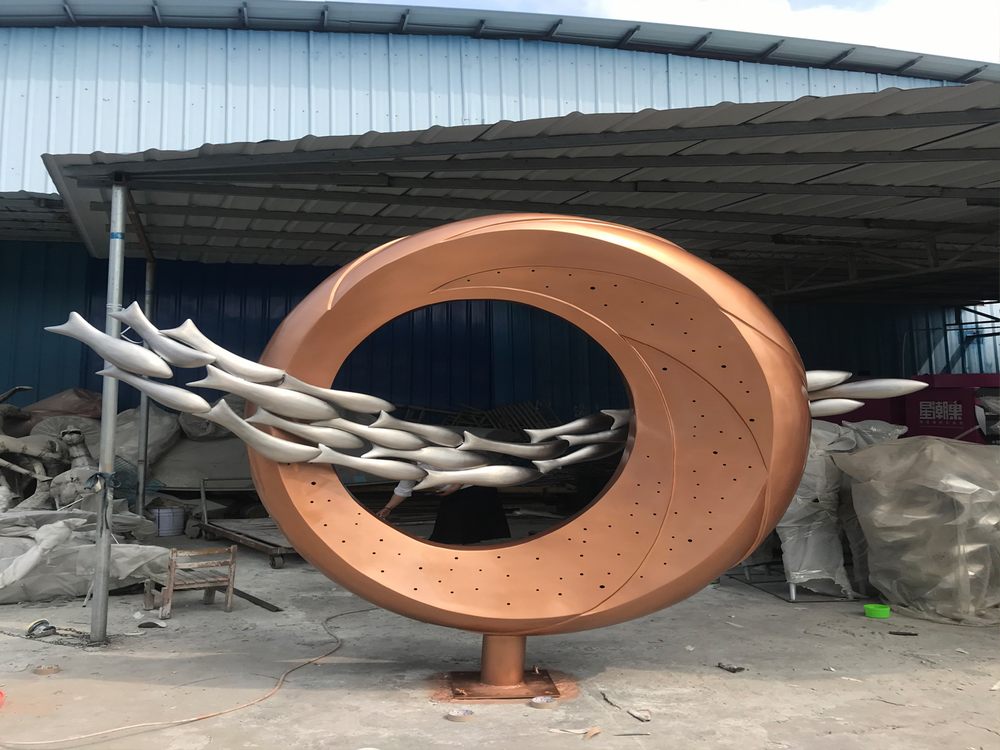
Porcelain sculptures captivate with their delicate beauty, and the choice between a matte or glossy finish significantly impacts their aesthetic appeal. Artists achieve these distinct surface effects through a combination of specialized materials, glazing techniques, and firing processes.
For a glossy finish, artists typically apply a transparent or colored glaze containing silica and fluxes that melt during kiln firing, creating a smooth, reflective surface. Multiple glaze layers or a high-gloss clear coat can enhance the shine. The firing temperature plays a crucial role, with most glossy finishes requiring temperatures between 1200-1400°C to properly vitrify.
Matte finishes result from alternative approaches. Some artists use matte-specific glazes containing materials like calcium or magnesium that crystallize during cooling, scattering light diffusely. Others achieve matte effects through surface treatments - applying wax resist before glazing, sandblasting after firing, or using underglazes with minimal clear coating. A third method involves controlled reduction firing, where limited oxygen creates subtle surface textures.
Contemporary artists often combine techniques, creating contrast by leaving some areas unglazed (bisque) while glazing others. The choice between matte and glossy ultimately depends on the desired artistic expression - glossy finishes emphasize vibrancy and depth, while matte surfaces convey subtlety and tactile quality. Mastery of these techniques allows porcelain artists to precisely control their work's final appearance and emotional impact.