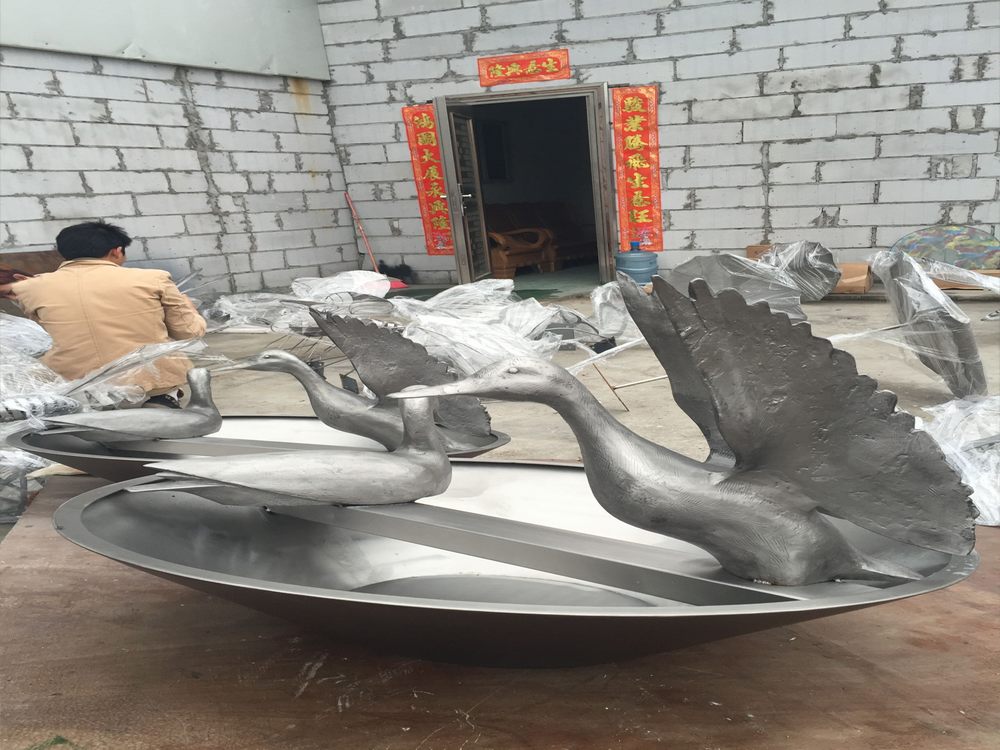
Choosing the right kiln for porcelain sculpture production is crucial for achieving high-quality results. The first consideration is temperature control, as porcelain requires consistent high temperatures (typically 1200-1400°C) for proper vitrification. Look for a kiln with precise digital controllers and reliable thermocouples.
Kiln size is another critical factor. Ensure the interior space accommodates your largest sculptures while allowing even heat distribution. A too-small kiln may restrict creativity, while an oversized one wastes energy.
The type of kiln matters too. Electric kilns are popular for their ease of use and clean operation, while gas kilns offer unique atmospheric effects. Consider oxidation versus reduction firing capabilities based on your desired finishes.
Heating elements and insulation quality directly impact performance and longevity. High-quality elements maintain temperature efficiently, and good insulation reduces firing times and energy costs.
Finally, evaluate safety features, ventilation requirements, and your studio's power capacity. Investing in the right kiln from the beginning will save time, money, and frustration in your porcelain sculpture journey.