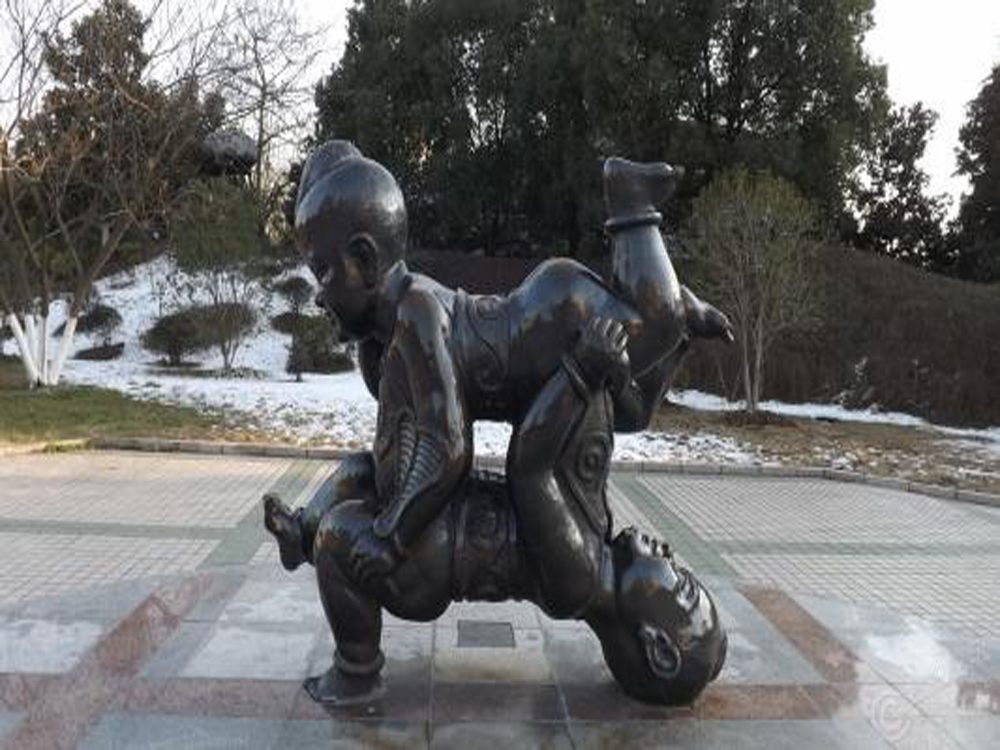
Porcelain sculptures are delicate works of art, but they are prone to several common defects during creation and firing. Understanding these issues and their solutions ensures higher-quality results.
1. Cracking: Cracks often occur due to uneven drying or rapid temperature changes in the kiln. To prevent this, ensure slow, even drying and controlled firing cycles.
2. Glaze Imperfections: Bubbles, pinholes, or uneven glaze application can mar the surface. Proper glaze mixing, consistent application, and correct firing temperatures help avoid these flaws.
3. Warping: Uneven thickness or improper support during firing causes warping. Design sculptures with balanced thickness and use kiln stilts for stability.
4. Color Inconsistencies: Fading or uneven colors result from incorrect pigment ratios or firing conditions. Test glazes and maintain precise kiln settings.
5. Structural Weakness: Thin or poorly joined parts may break. Reinforce weak areas with slip or adjust clay composition for better durability.
By mastering these techniques, artists can minimize defects and create stunning, long-lasting porcelain sculptures.