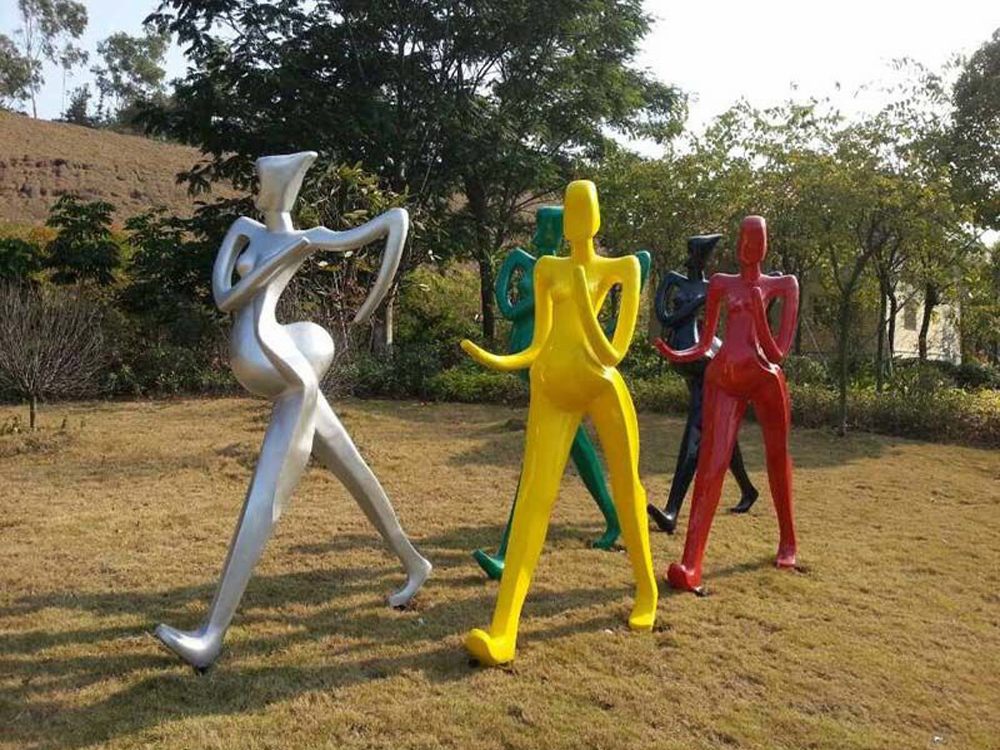
Creating painted porcelain sculptures with consistent colors across multiple batches is a meticulous process that requires precision, expertise, and careful planning. Artists employ several techniques to ensure uniformity.
First, they use standardized glaze formulas, meticulously recording pigment ratios and firing temperatures. This ensures each batch replicates the intended hues. Many artists create custom color charts or swatches for reference, allowing them to match shades accurately.
Second, controlled firing conditions are critical. Even slight variations in kiln temperature or firing duration can alter colors. Artists often use programmable kilns with precise temperature controls and monitor each firing cycle closely.
Third, batch testing is common. Before producing a full series, artists create test pieces to verify color outcomes. Adjustments are made to glazes or techniques if discrepancies arise.
Finally, experienced artists often hand-mix their pigments rather than relying on pre-mixed commercial glazes. This allows for finer control over color intensity and tone. Some even apply colors in multiple thin layers, building up the desired shade gradually for greater consistency.
By combining these methods, artists can produce porcelain sculptures with remarkably consistent coloring, even when created months or years apart. This attention to detail is what distinguishes fine art porcelain from mass-produced pieces.