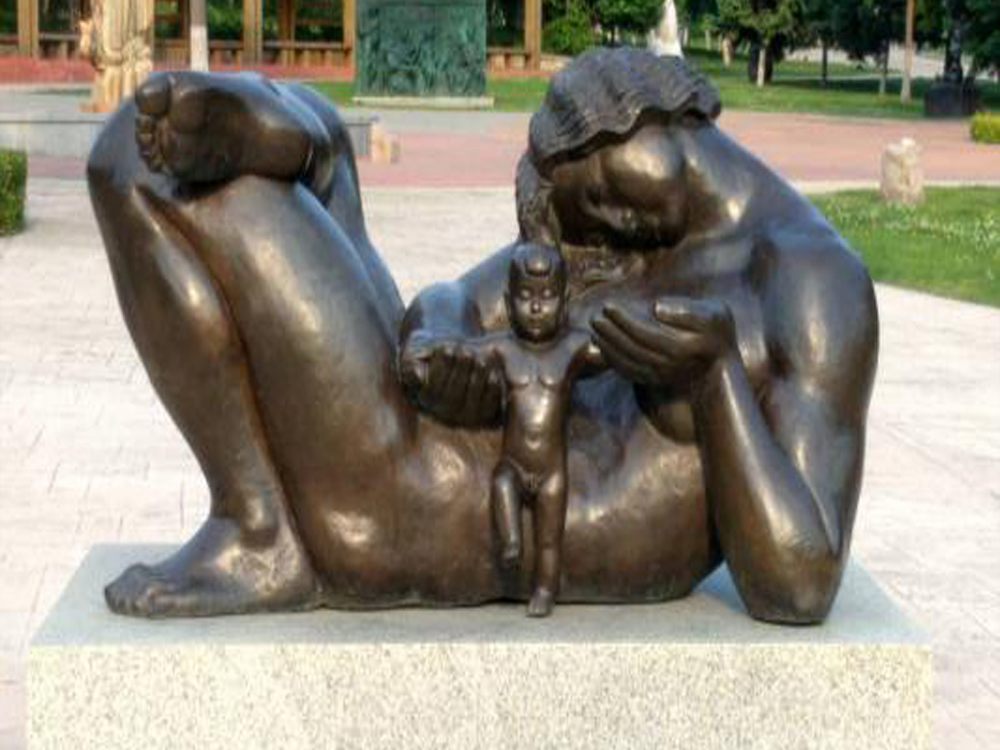
Creating a uniform series of porcelain sculptures requires meticulous planning and execution. Artists often begin by designing a master model, which serves as the blueprint for consistency. This model is then used to create precise molds, ensuring each piece retains identical proportions and details.
Material consistency is equally critical. Artists carefully select and prepare clay batches to maintain uniform texture and shrinkage rates during firing. Glazing techniques are standardized, with controlled application methods and firing temperatures to achieve matching finishes across the series.
Many artists employ jig systems for repetitive processes like attaching limbs or decorative elements. Some utilize digital tools like 3D scanning to verify dimensional accuracy between pieces. The most successful series balance technical precision with artistic expression, maintaining individuality within the framework of uniformity.
Seasoned ceramicists often document every step in detail, creating a repeatable workflow that preserves the series' cohesive aesthetic while allowing for subtle variations that give each piece its unique character within the set.