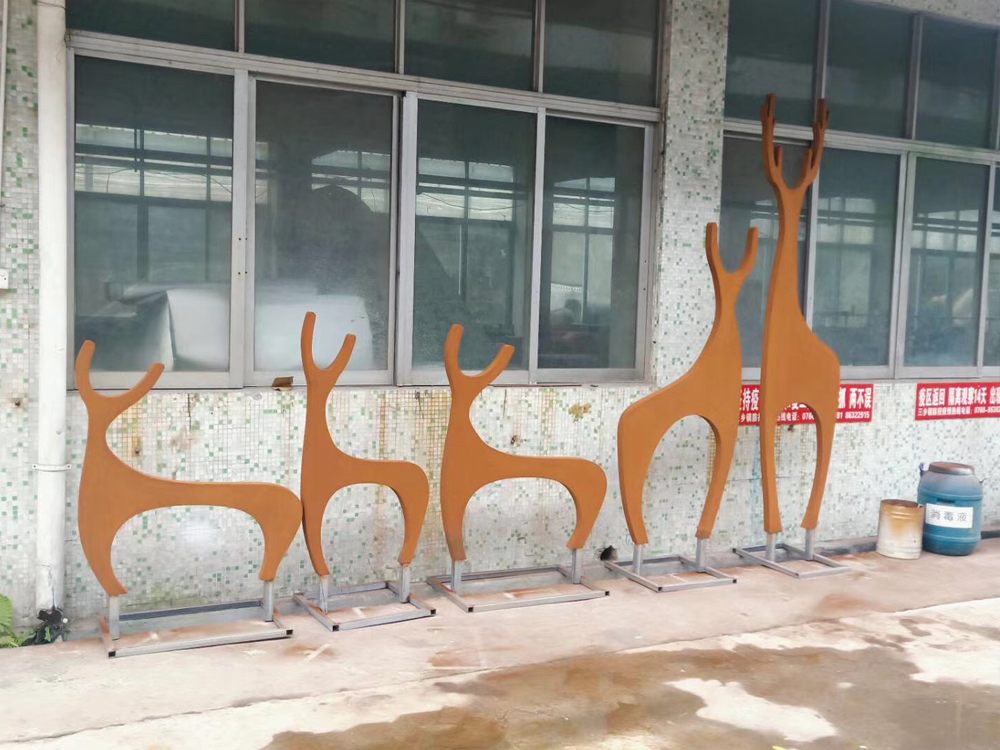
The fusion of modern technology like 3D printing with traditional porcelain sculpture is reshaping the ceramic art landscape. Artists now leverage digital tools to push boundaries while preserving centuries-old craftsmanship.
3D printing enables unprecedented precision in porcelain production. Sculptors first design intricate models using CAD software, allowing for complex geometries impossible with hand-building. The printer then layers fine ceramic paste, building forms with micron-level accuracy. This hybrid approach reduces material waste and accelerates prototyping—a game-changer for limited editions.
Traditional artisans integrate these innovations thoughtfully. Many use 3D-printed elements as armatures for hand-sculpted details, combining machine precision with organic textures. Glaze application remains manual, ensuring each piece retains unique kiln-fired character. Some pioneers even modify printers to extrude custom porcelain blends matching historic recipes.
The technology also democratizes porcelain art. Digital files allow global collaboration between ceramicists, while museums employ 3D scanning to recreate fragile antiquities. However, purists argue the soul of porcelain lies in direct clay manipulation—a tension driving fascinating artistic dialogues.
From conceptual installations to functional ware, this technological synergy expands porcelain's possibilities while honoring its heritage. As artists continue experimenting, 3D printing emerges not as a replacement, but as a transformative tool in ceramic evolution.