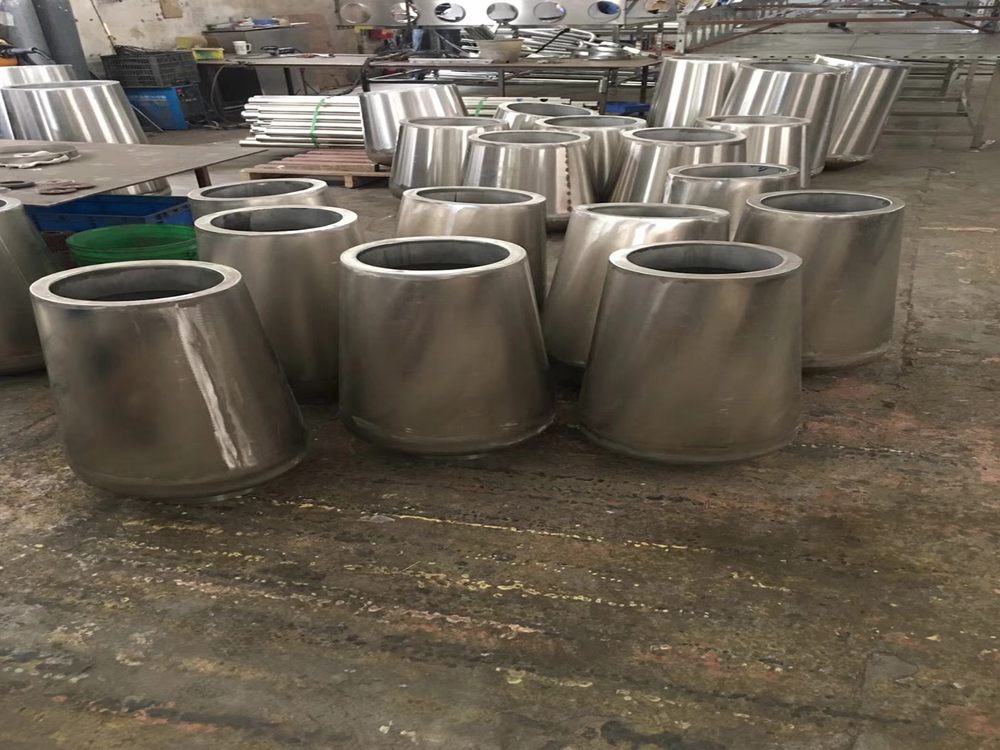
Creating large-scale porcelain sculptures without structural weaknesses is a complex endeavor that demands meticulous craftsmanship and technical expertise. Porcelain, while prized for its delicate beauty, presents several challenges due to its inherent fragility and susceptibility to cracking.
One major hurdle is the material's low plasticity, making it difficult to shape into large forms without collapsing. Artists often reinforce the clay with additives or use armatures, but these solutions can compromise the sculpture's purity. The drying process is another critical phase; uneven shrinkage can lead to warping or fractures. Controlled drying environments and gradual moisture reduction are essential to prevent these issues.
Firing large porcelain pieces introduces further complications. Thermal stress during kiln firing can cause cracks or even explosions if the piece isn't evenly heated. Multi-stage firing and precise temperature control are necessary to ensure durability. Additionally, the weight of large sculptures strains the material, requiring careful engineering to distribute stress and avoid weak points.
Despite these challenges, advancements in ceramic technology and innovative techniques continue to push the boundaries of porcelain art, enabling artists to create breathtaking, durable masterpieces.