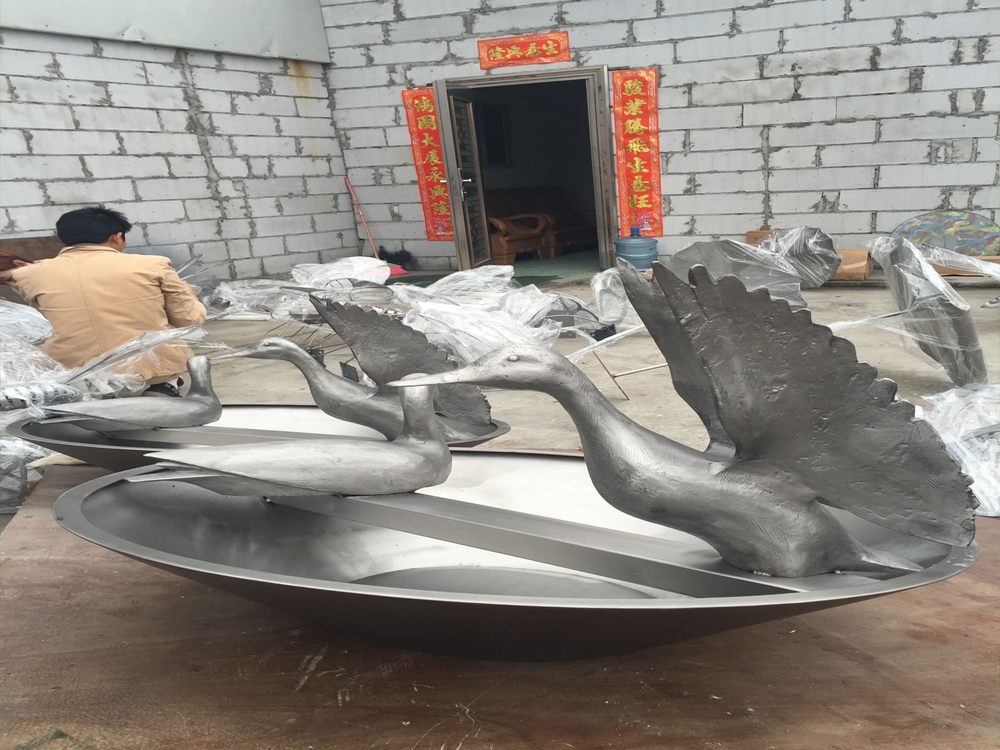
Achieving uniform glaze colors across multiple batches of porcelain sculptures is a complex process fraught with challenges. One major hurdle lies in raw material variations—even slight differences in mineral composition or particle size can dramatically alter final hues. Firing conditions present another critical variable, as temperature fluctuations as small as 10°C can shift color outcomes. The chemical interaction between glaze components and clay bodies often creates unexpected results, particularly when working with reduction firing techniques that rely on precise oxygen levels.
Master artisans must also contend with the "memory effect" of kilns, where previous firings influence subsequent results. Additionally, glaze application thickness—often varying by just hundredths of a millimeter—can transform color saturation and texture. Many studios implement rigorous quality control measures, including standardized mixing protocols, computerized kiln monitoring, and test tile systems. However, the organic nature of ceramic materials means some variation remains inevitable, requiring artists to embrace the subtle beauty of handmade uniqueness while striving for technical perfection.
Advanced solutions now include spectral analysis for glaze recipes and machine learning algorithms that predict color outcomes based on historical firing data. Yet despite technological advances, the alchemy of perfect glaze consistency continues to demand both scientific precision and artistic intuition.