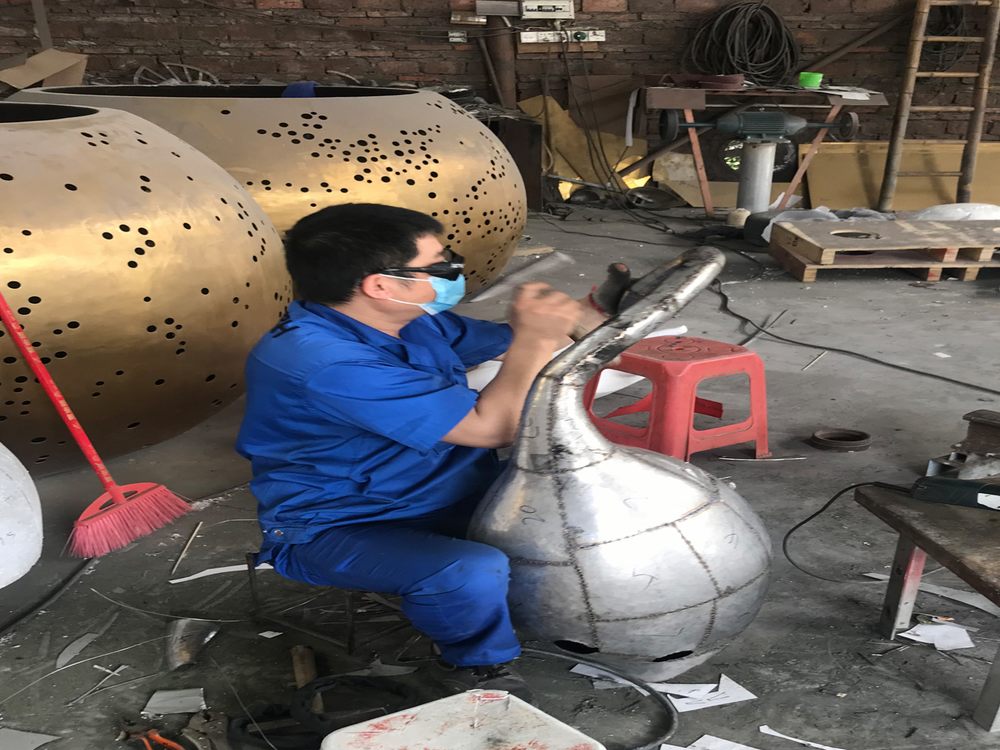
The art of creating handmade porcelain sculptures is a delicate dance between tradition and innovation. As demand grows, artisans and manufacturers face significant challenges in scaling production without sacrificing the meticulous craftsmanship that defines these pieces.
1. Skilled Labor Shortages: Each sculpture requires highly trained artisans for intricate detailing, and replicating this expertise across a larger workforce is time-consuming and costly.
2. Material Consistency: Natural clay variations can affect texture and color, making uniform quality difficult when sourcing larger quantities.
3. Kiln Capacity Limitations: Firing processes are sensitive; overcrowded kilns risk uneven heat distribution, leading to cracks or glaze imperfections.
4. Time-Intensive Processes: Hand-painting and carving cannot be rushed, creating bottlenecks when trying to increase output.
5. Quality Control Complexity: Every piece must be individually inspected, requiring meticulous attention that scales poorly with higher volumes.
Solutions like modular training programs, advanced clay purification, and staggered kiln scheduling are being explored, but the essence of handmade artistry remains at odds with industrial efficiency. The true challenge lies in preserving the soul of each sculpture while meeting commercial demands—a balance that continues to test even the most experienced porcelain studios.