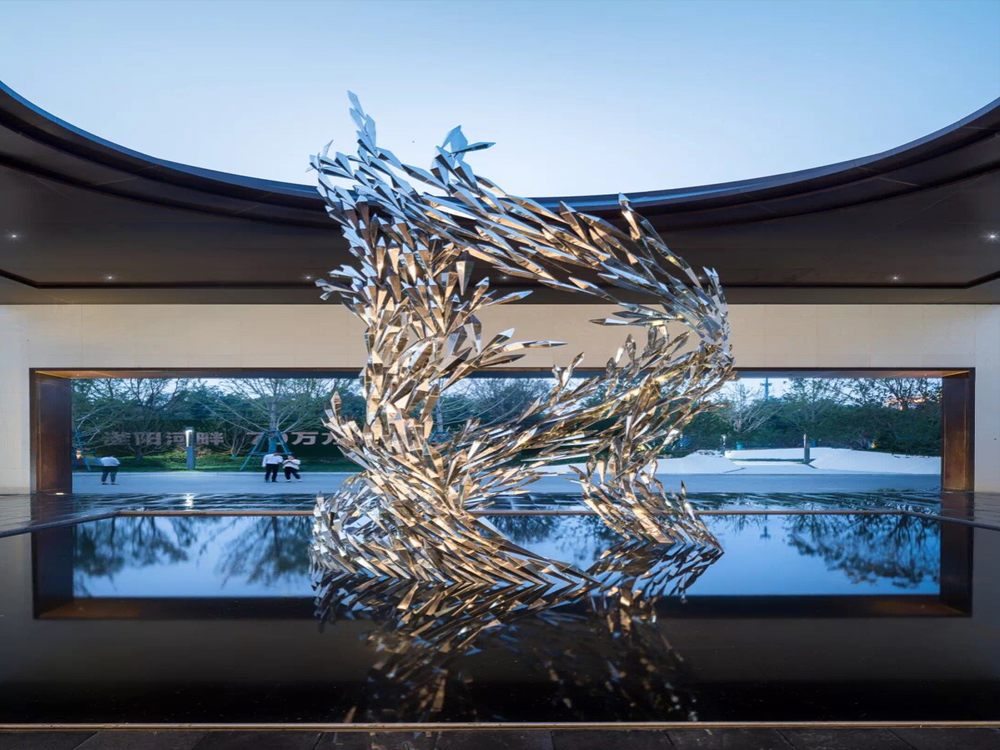
The delicate art of porcelain sculpture faces unprecedented challenges as global material shortages reshape production landscapes. Skilled artisans now confront limited access to high-quality kaolin clay, the essential "white gold" of porcelain making, forcing many to compromise on purity or seek inferior substitutes. Glaze components like cobalt oxide and feldspar have become unpredictable commodities, disrupting centuries-old recipes perfected over generations.
Production timelines stretch unpredictably as studios wait months for basic materials that previously took weeks to procure. Master sculptors report wasting up to 30% more material due to inconsistent clay quality, while emerging artists struggle with prohibitive material costs. The shortage crisis particularly threatens intricate techniques like paper-thin porcelain and elaborate glazing methods requiring specific chemical compositions.
Some workshops adapt by developing hybrid clay blends or recycling production waste, though purists argue this compromises artistic integrity. Larger manufacturers stockpile materials, creating secondary market inflation that prices out independent artists. Conservationists worry about deteriorating quality in contemporary pieces that future generations may study.
Innovative solutions are emerging, including 3D-printed clay alternatives and bio-engineered materials, though traditionalists resist these modern approaches. The crisis ultimately forces the porcelain community to re-examine sustainable practices while preserving the art form's exquisite legacy. As material scarcity becomes the new normal, adaptability may define the next chapter of porcelain artistry.