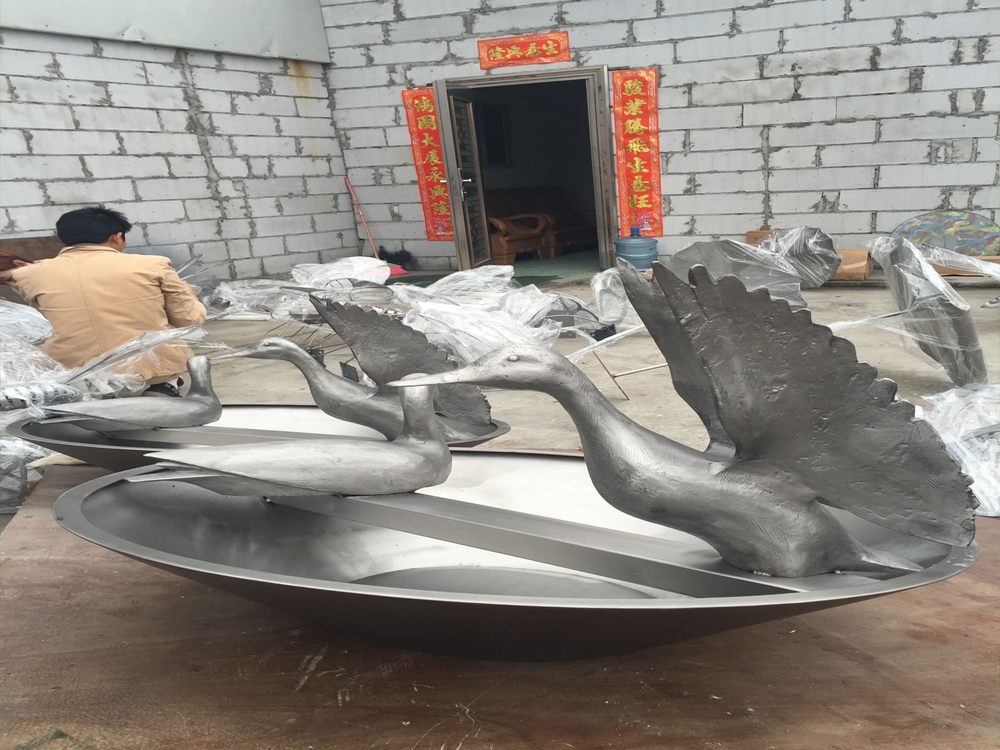
Creating porcelain sculptures with embedded elements is a delicate and complex art form that requires meticulous attention to detail. One of the most common challenges is ensuring material compatibility between the porcelain and the embedded elements, such as metals or glass. Differences in thermal expansion rates can lead to cracking or warping during the firing process.
Another significant hurdle is achieving precise placement of the embedded elements. Porcelain shrinks significantly during firing, making it difficult to predict the final position of the inclusions. Artists must carefully calculate shrinkage rates and adjust their designs accordingly.
The firing process itself poses multiple challenges. Porcelain requires high temperatures, which can damage or alter embedded materials. Controlling the kiln environment to prevent oxidation or other chemical reactions is crucial. Additionally, the cooling phase must be managed to avoid thermal shock, which can cause fractures.
Finally, the fragility of porcelain adds another layer of difficulty. Embedded elements can create weak points in the structure, making the sculpture more prone to breakage. Artists often need to reinforce these areas without compromising the aesthetic integrity of the piece.
Despite these challenges, mastering the techniques to overcome them can result in stunning, unique artworks that showcase the beauty and versatility of porcelain.