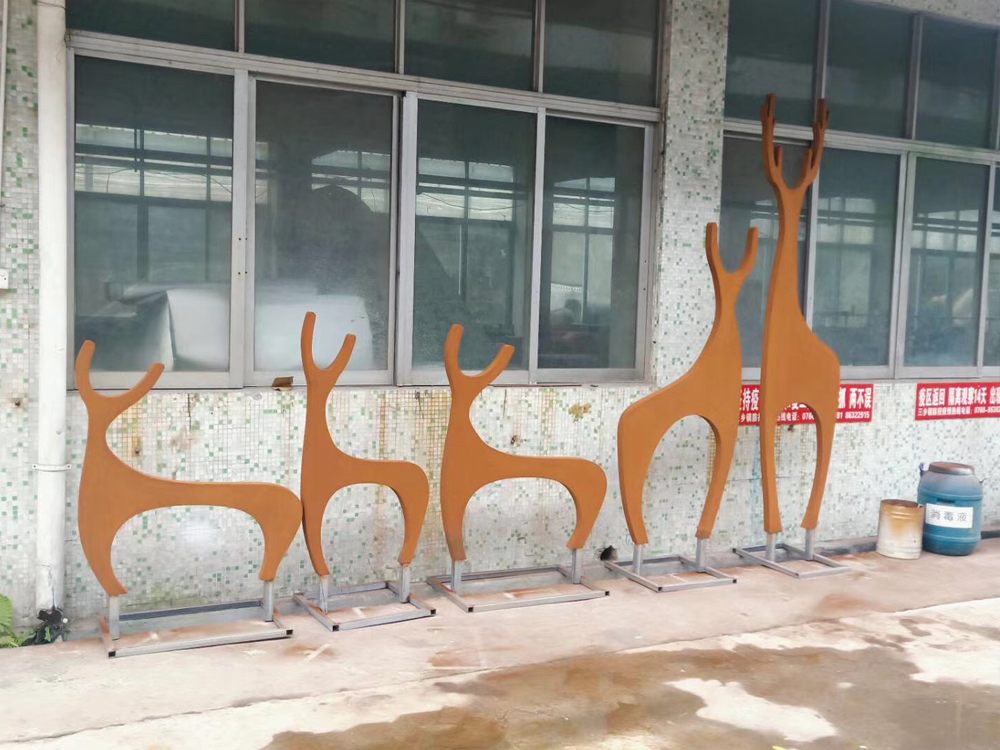
The firing process is a critical stage in creating porcelain sculptures, but it often introduces various types of damage due to high temperatures and material reactions. One of the most frequent issues is cracking, which can occur from rapid temperature changes or uneven heating. Thermal shock causes hairline fractures or even complete breaks, especially in thicker sections.
Glaze defects are another common problem, including crawling (where glaze pulls away from the surface), blistering (bubbles forming under the glaze), or pinholing (tiny holes in the glaze layer). These often result from improper glaze application or firing schedules.
Warping and slumping occur when the sculpture loses structural integrity under heat, causing distortions in shape. This is particularly common in asymmetrical or thinly-walled designs. Additionally, kiln-related issues like underfiring or overfiring can lead to weak bonding or excessive vitrification, compromising durability.
Preventive measures include controlled kiln ramping, proper clay preparation, and precise glaze formulations. Understanding these risks helps artists minimize damage and achieve flawless porcelain creations.