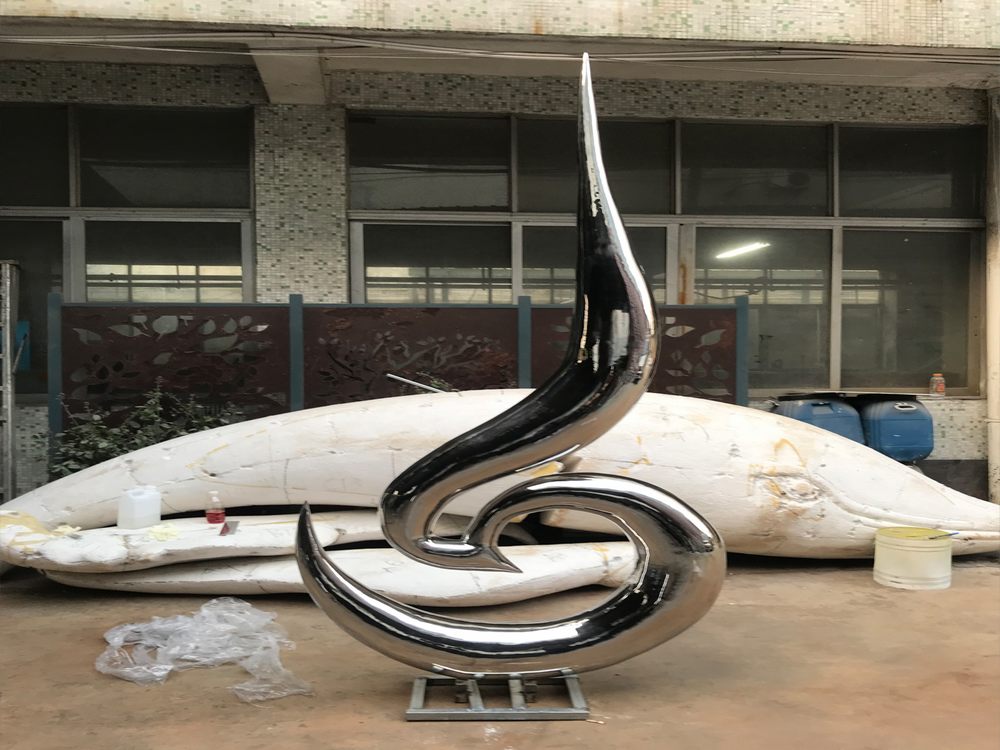
Creating porcelain sculptures with intricate, three-dimensional patterns is a demanding art form that combines technical skill and artistic vision. One major challenge is the fragility of porcelain itself, which requires meticulous handling during shaping and drying to avoid cracks or deformities. The complexity of 3D designs amplifies this difficulty, as thin protruding elements are especially vulnerable.
Another hurdle lies in the precision required for pattern transfer. Unlike flat surfaces, three-dimensional forms demand careful planning to ensure designs remain proportionate when wrapped around curves or overlapping sections. Artists often struggle with distortion during the clay's shrinkage in drying and firing stages, which can alter delicate details.
The firing process presents further obstacles. High kiln temperatures (typically 1200-1400°C) can cause intricate elements to warp or melt if not properly supported. Glazing compounds these challenges, as viscous liquids may pool unevenly in recessed areas while failing to adhere properly to raised patterns.
Time sensitivity adds pressure throughout creation. Porcelain remains workable for limited periods before becoming too dry to manipulate, forcing artists to complete complex patterning in constrained windows. This demands both speed and absolute precision - a difficult balance to maintain.
Despite these challenges, successful execution results in breathtaking artworks that showcase porcelain's luminous quality through multidimensional designs. Mastering these difficulties separates exceptional ceramic artists from novices, making such sculptures particularly prized in the art world.