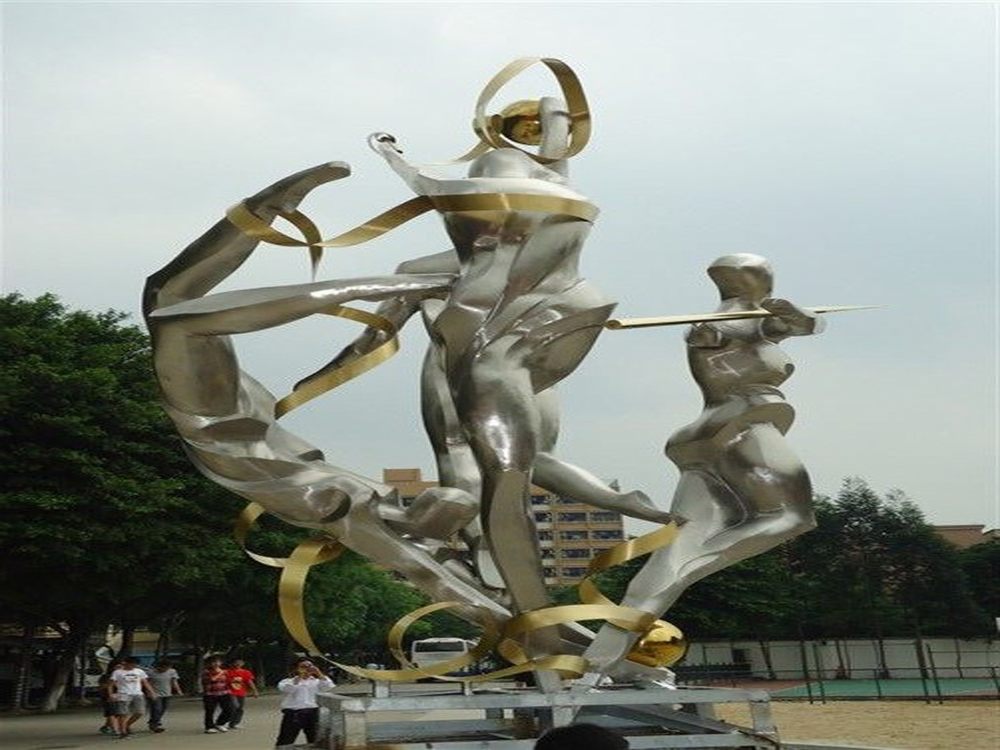
Mass-producing porcelain sculptures without compromising artistic integrity presents a unique set of challenges. The delicate nature of porcelain, combined with the intricate craftsmanship required, makes scaling production difficult while maintaining the original artistic vision.
One major challenge is replicating fine details consistently. Handcrafted porcelain sculptures often feature delicate textures and subtle imperfections that contribute to their charm. Industrial molds and automated processes may struggle to capture these nuances, resulting in a loss of artistic authenticity.
Material consistency is another hurdle. Porcelain's composition and firing process significantly impact the final product. Variations in clay quality, kiln temperatures, or glaze application can lead to inconsistencies, making it hard to produce uniform yet artistically valid pieces.
Artistic oversight diminishes in mass production. Unlike one-of-a-kind creations, large-scale manufacturing often prioritizes efficiency over artistry. Ensuring that each piece retains the sculptor's intended expression requires careful quality control and skilled artisans at every stage.
Cost constraints further complicate the process. High-quality materials and meticulous craftsmanship are expensive, and cutting corners to reduce costs can degrade the final product's aesthetic and structural integrity.
Ultimately, balancing artistic integrity with industrial efficiency demands collaboration between artists and manufacturers, innovative techniques, and a commitment to preserving the soul of each sculpture—even in mass production.