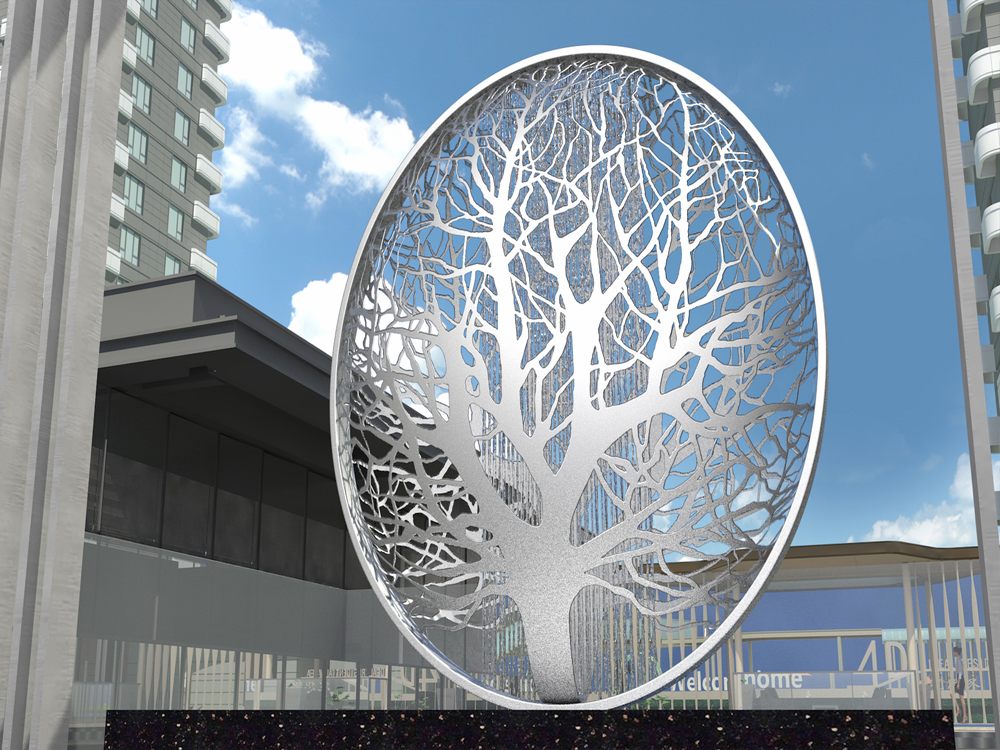
Porcelain sculptures are revered for their delicate beauty and intricate craftsmanship, but ensuring their quality before they reach the market involves a meticulous testing process. Manufacturers employ multiple quality control measures to guarantee each piece meets industry standards.
1. Visual Inspection: Every sculpture undergoes a thorough visual examination to identify surface flaws such as cracks, glaze inconsistencies, or uneven coloring. Skilled artisans scrutinize details under bright lighting to ensure perfection.
2. Thermal Shock Testing: Porcelain must withstand sudden temperature changes without cracking. Samples are subjected to rapid heating and cooling cycles to verify durability, especially for functional or decorative pieces exposed to varying environments.
3. Structural Integrity Checks: Sculptures are tapped lightly to detect hidden fractures or weak points. Hollow pieces are inspected for uniform wall thickness to prevent breakage.
4. Glaze and Finish Testing: The glaze’s adherence and smoothness are tested using specialized tools. Acid resistance tests may also be conducted to ensure longevity.
5. Craftsmanship Verification: Each piece is compared against design specifications to confirm precision in shaping, detailing, and proportions.
Only after passing these rigorous tests are porcelain sculptures deemed market-ready, ensuring collectors and buyers receive flawless, high-quality art pieces.