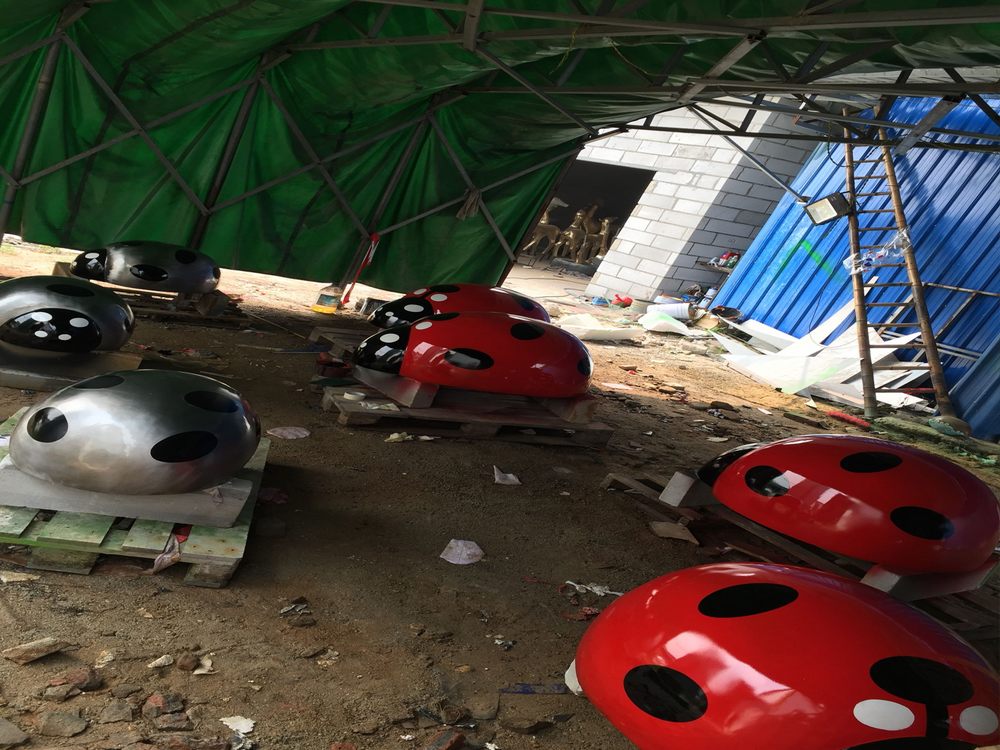
Porcelain sculpture production is a delicate and intricate art form that demands precision at every stage. While the process varies by technique and style, certain critical stages are particularly prone to errors, often leading to costly or irreparable damage.
1. Clay Preparation and Wedging
The foundation of any porcelain sculpture lies in the quality of the clay. Improper wedging—kneading to remove air bubbles—can result in cracks or explosions during firing. Inconsistent moisture levels or contaminants in the clay also lead to structural weaknesses.
2. Shaping and Sculpting
Hand-building or wheel-throwing requires meticulous attention. Uneven thickness, weak joints, or rushed drying can cause warping or collapse. Overworking the clay may introduce stress points that fail later.
3. Drying Phase
Controlled drying is essential. Rapid drying causes cracks, while uneven drying leads to distortion. Large or complex pieces are especially vulnerable if not dried slowly and uniformly.
4. Bisque Firing
The first firing transforms fragile clay into porous bisque. Temperature spikes or uneven heat distribution can cause fractures or bloating. Overfiring may vitrify the piece prematurely, making glazing difficult.
5. Glazing Application
Uneven glaze thickness, drips, or air bubbles create flaws in the final finish. Contamination (like fingerprints or dust) can cause blemishes, while improper glaze chemistry may lead to crawling or peeling.
6. Final Firing
The high-temperature glaze firing is the most unforgiving stage. Thermal shock, incorrect kiln atmosphere, or over/under-firing can ruin weeks of work—resulting in cracks, discoloration, or glaze defects like pinholes.
To minimize errors, artisans must prioritize patience, precise tool use, and strict kiln monitoring. Mastery of these stages separates functional art from fragile failures.