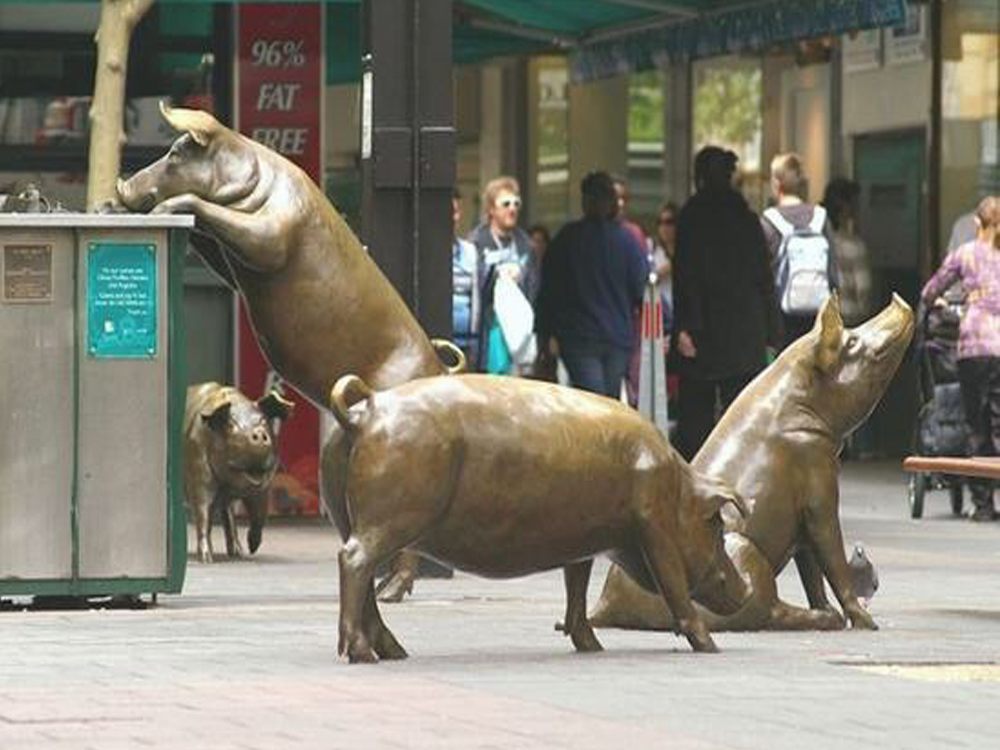
The drying time for porcelain sculpture components is influenced by several critical factors, each playing a vital role in ensuring the final product's quality and structural integrity.
1. Clay Thickness: Thicker clay sections retain moisture longer, requiring extended drying periods to prevent cracking. Thin layers dry faster but need careful monitoring to avoid uneven shrinkage.
2. Humidity Levels: High humidity slows evaporation, prolonging drying time. Controlled environments with moderate humidity (40-60%) are ideal for consistent results.
3. Airflow and Ventilation: Proper airflow accelerates drying by evenly distributing moisture. Stagnant air can lead to uneven drying and defects.
4. Kiln Temperature and Settings: Pre-drying in a kiln at low temperatures (100-200°F) can reduce overall drying time, but abrupt temperature changes risk cracking.
5. Clay Composition: Porcelain’s fine particle size retains water longer than coarser clays. Additives like grog may speed up drying but alter texture.
6. Ambient Temperature: Warmer environments expedite drying, while cooler conditions delay it. Consistency is key to avoiding stress fractures.
By balancing these factors, artists and manufacturers can optimize drying times, ensuring durable, high-quality porcelain sculptures.