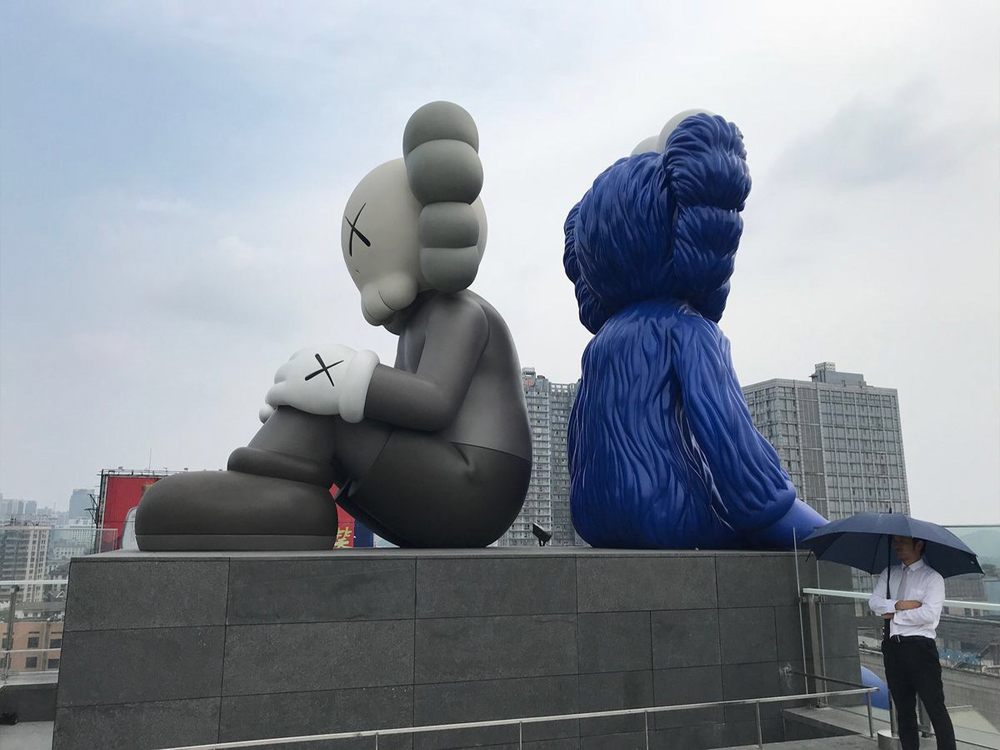
Creating hollow porcelain sculptures is a delicate balance of artistry and engineering. To ensure structural integrity, artists employ several specialized techniques. First, they carefully select and prepare the clay, often blending materials to enhance strength and reduce shrinkage. The walls of the sculpture are kept uniformly thin to prevent cracking during drying and firing.
Internal supports, such as temporary clay struts or removable foam cores, are used during construction to maintain shape. These are later extracted once the piece is partially dried. Kiln firing is meticulously controlled, with gradual temperature changes to avoid thermal shock. Some artists also use slip trailing or additional clay layers at stress points for reinforcement.
Advanced designs incorporate strategic hollowing to distribute weight evenly, while textured surfaces can disguise structural seams. Mastery of these methods allows porcelain artists to create breathtaking, durable hollow forms that defy the material's inherent fragility.