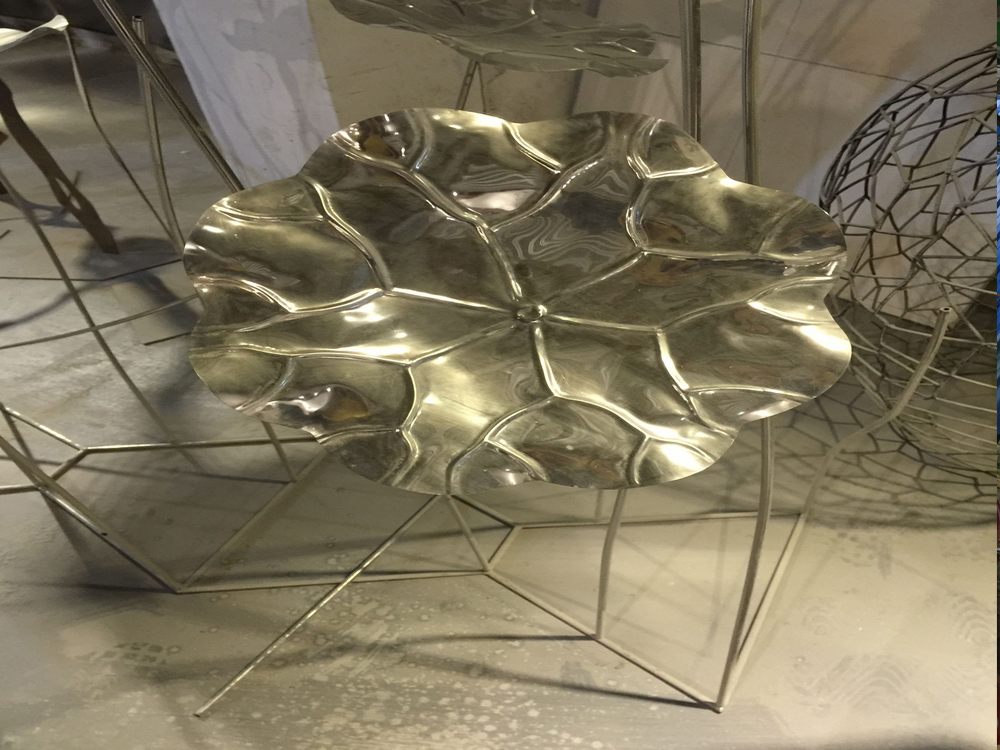
Creating porcelain sculptures with delicate protrusions is a complex art form that demands precision, patience, and specialized techniques. Artists begin by carefully selecting high-quality porcelain clay, known for its fine particle structure and plasticity, which allows for intricate detailing.
To address the challenge of fragile extensions, many sculptors employ armatures or temporary supports made of wire or wax during the shaping process. These are later removed or melt away during firing. The drying phase is critical; controlled humidity environments prevent cracking as the piece loses moisture unevenly due to varying thicknesses.
Advanced artists often work in stages, building up protrusions gradually with slip (liquid clay) and scoring each connection point meticulously. Some use paper clay mixtures containing cellulose fibers for added strength in thin projections.
Kiln firing presents the ultimate test. Porcelain's high shrinkage rate (up to 20%) requires precise temperature ramping. Many creators bisque fire at lower temperatures first, then apply glazes and fire again. For extreme projections, some artists develop custom kiln furniture or use refractory supports to prevent warping.
Contemporary solutions include 3D-printed porcelain and hybrid techniques where delicate elements are cast separately and assembled post-firing. Regardless of method, successful execution combines material science with artistic vision, transforming porcelain's inherent fragility into breathtaking strength.