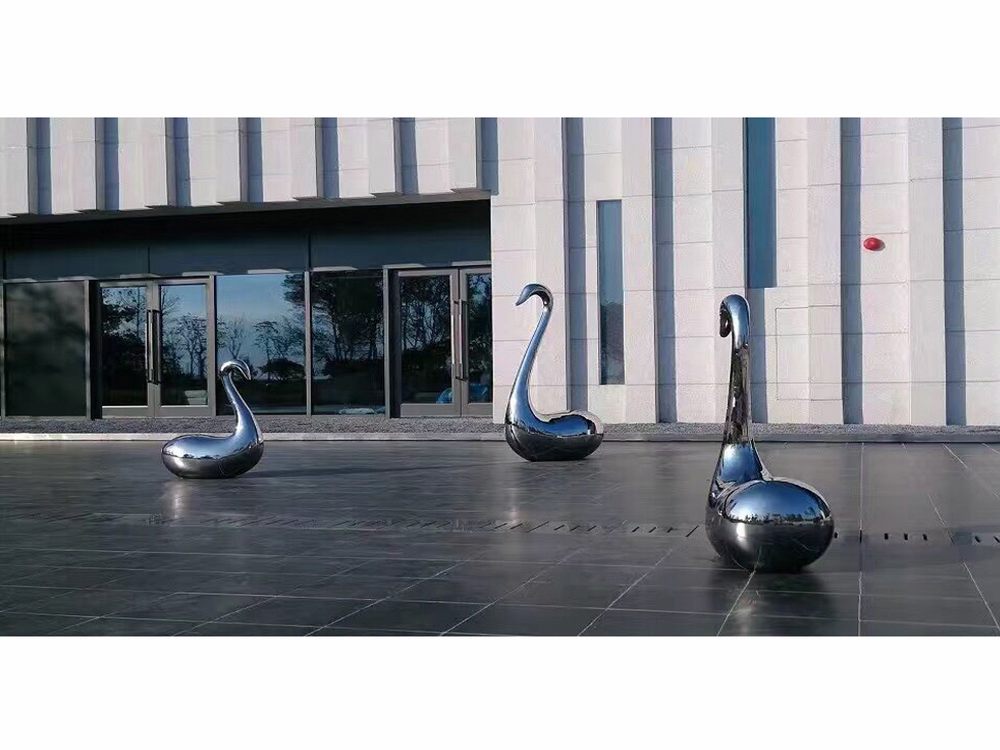
Creating large porcelain sculpture installations presents unique challenges, particularly in managing weight to ensure structural integrity and visual impact. Artists employ a variety of innovative techniques to address these issues while maintaining the delicate beauty of porcelain.
One common approach is the use of hollow construction. By carefully designing sculptures with internal cavities, artists significantly reduce weight without compromising strength. This technique requires precise calculations to balance thin walls for lightness with sufficient thickness for durability.
Material selection also plays a crucial role. Many artists mix porcelain with other ceramic materials or additives that enhance strength-to-weight ratios. Some incorporate lightweight armatures or internal support systems made from materials like stainless steel or aluminum, carefully hidden within the ceramic form.
Modular design has emerged as another effective solution. Instead of creating massive single pieces, artists build installations from interconnected smaller components. This approach not only manages weight distribution but also facilitates transportation and installation.
Advanced drying and firing techniques help prevent structural weaknesses. Slow, controlled drying processes minimize stress points, while specialized kiln furniture supports pieces during firing to prevent deformation under their own weight.
Contemporary artists are also exploring digital fabrication methods. 3D modeling allows for precise weight distribution calculations before creation, while 3D printing with porcelain compounds enables testing of structural concepts at smaller scales.
The intersection of artistic vision and engineering principles continues to evolve in porcelain sculpture, with each new installation pushing the boundaries of what's possible with this demanding yet exquisite medium.