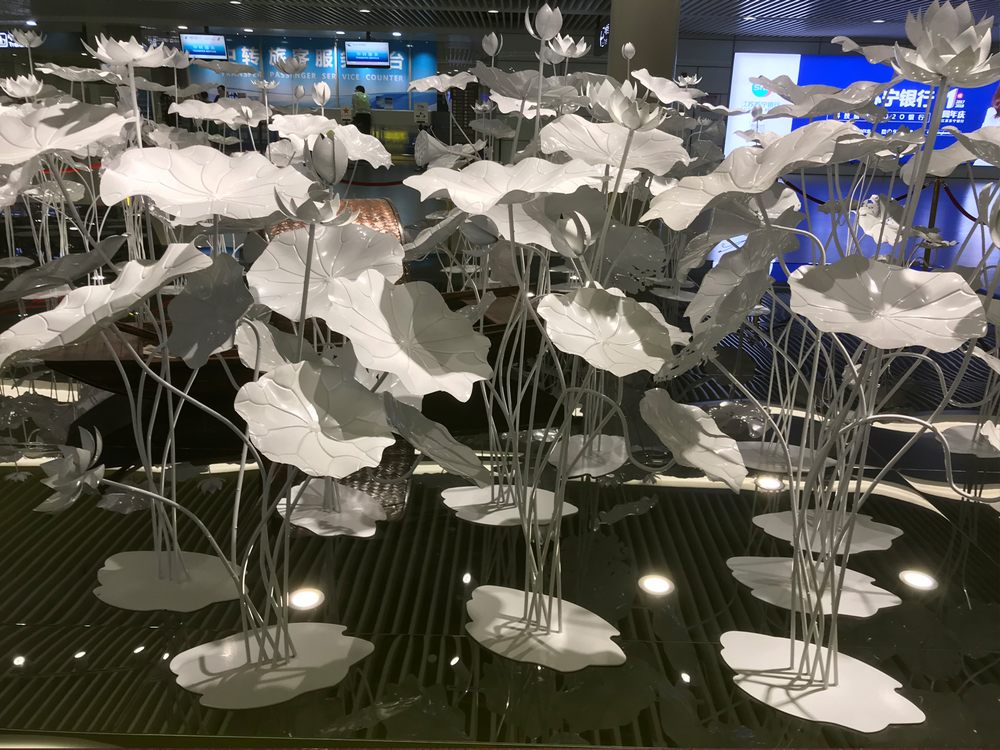
Managing the drying time of porcelain is a delicate yet critical process for ceramic artists to prevent cracks before firing. The key lies in balancing moisture evaporation while minimizing stress within the clay body. Experienced artists employ several proven techniques:
1. Slow, Even Drying: Wrapping pieces in plastic or placing them in damp boxes allows gradual moisture release over days or weeks. This prevents rapid shrinkage that causes cracks.
2. Controlled Environment: Maintaining stable humidity (40-60%) and avoiding direct airflow ensures uniform drying. Many artists use drying cabinets with adjustable ventilation.
3. Strategic Thickness: Uniform wall thickness prevents uneven drying rates. Artists often hollow out thick sections or add scoring to relieve tension.
4. Compression Techniques: Proper wedging and kneading eliminate air pockets while aligning clay particles for more even drying.
5. Pre-Drying Inspection: Artists routinely check for developing cracks using raking light, repairing minor flaws with slurry before complete drying.
Advanced practitioners sometimes incorporate additives like paper fiber or grog to improve clay's structural integrity during drying. The final stage involves bone-dry testing—when clay feels room temperature and no longer cool to the touch—before safe firing. Mastering these methods allows artists to produce crack-free porcelain works with consistent results.