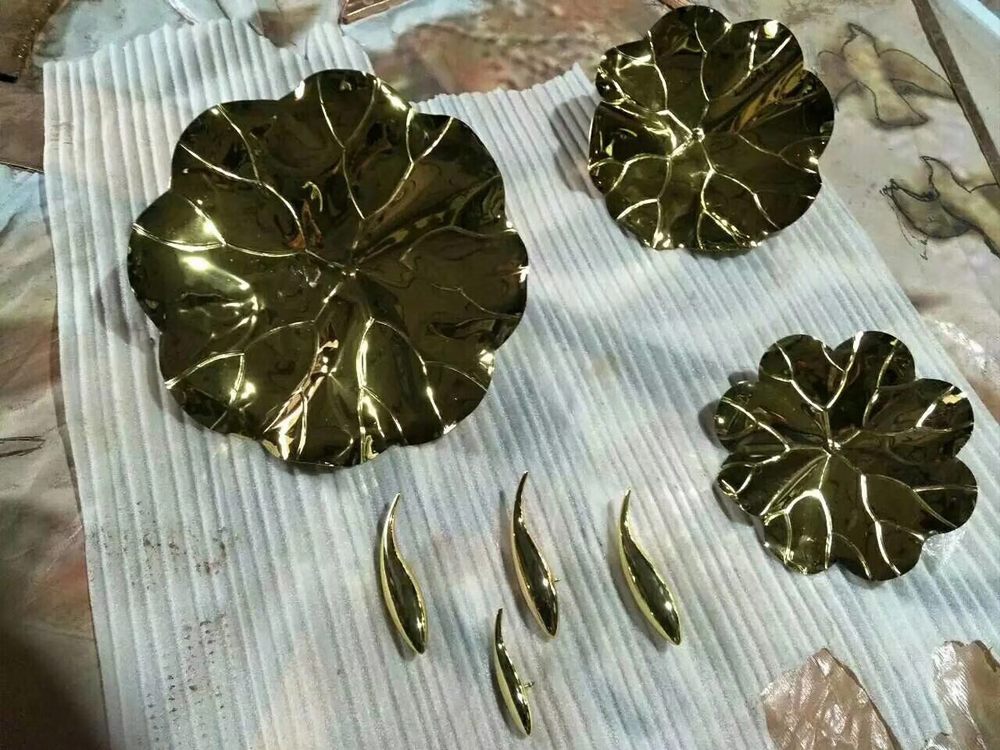
In the evolving world of ceramic art, contemporary artists are pioneering groundbreaking methods to fuse centuries-old porcelain techniques with cutting-edge digital fabrication. This hybrid approach begins with traditional material knowledge – mastering the properties of kaolin clay, glaze chemistry, and kiln firing – while incorporating digital tools like 3D modeling software and CNC milling.
Many creators start by digitally sculpting designs using programs like ZBrush or Blender, allowing for intricate geometries impossible to achieve by hand. These digital models then guide various fabrication methods: some artists use 3D printers with ceramic extruders to build forms layer by layer, while others employ robotic arms for precision carving of solid clay blocks.
The magic happens in the synthesis – digital precision meets artisan refinement. After digital fabrication, artists apply hand-finishing techniques: smoothing seams with traditional ribs, adjusting proportions with skilled fingers, and applying glazes using historic brush methods. The final firing process still relies on the alchemy of traditional kilns, where digital and manual elements permanently fuse into cohesive artworks.
This convergence creates unprecedented possibilities: delicate lattice structures with mathematical precision alongside organic, hand-touched surfaces. Artists like Olivier van Herpt have demonstrated how digital fabrication can actually enhance traditional aesthetics, producing pieces that honor porcelain's heritage while expanding its creative boundaries. The result is a new ceramic language that respects the past while embracing technological innovation.