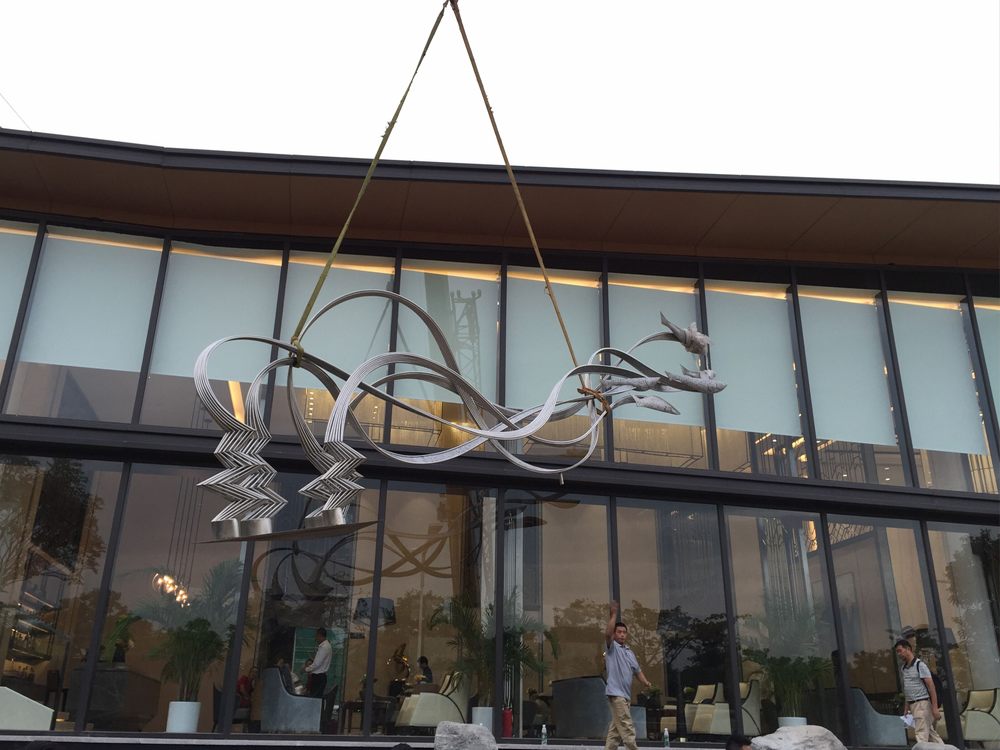
Creating porcelain sculptures for high-salinity environments presents unique artistic and technical challenges. One of the most significant issues is material durability. Porcelain, while elegant, is naturally porous, making it vulnerable to salt penetration. Over time, salt crystals can form within the clay body, causing cracks and structural weakening.
Another major challenge is glaze stability. Traditional glazes may react unpredictably to prolonged exposure to saltwater, leading to discoloration or peeling. Artists must experiment with specialized formulations to ensure long-term adhesion and visual appeal.
The sculpting process itself becomes more complex in such conditions. High salinity accelerates corrosion, requiring thicker walls or reinforced designs to prevent premature deterioration. Additionally, the drying and firing stages demand precise control to minimize microscopic flaws that salt could exploit.
Environmental factors also play a role. Temperature fluctuations in coastal areas can cause expansion and contraction stresses, while humidity variations affect the clay's workability. These variables require artists to adapt their techniques significantly compared to creating pieces for stable indoor environments.
Finally, there's the challenge of maintaining artistic integrity while meeting these technical demands. The need for durability often conflicts with delicate detailing, forcing sculptors to find innovative compromises between strength and aesthetic vision.
Overcoming these obstacles requires a blend of materials science expertise and artistic creativity, making porcelain sculpture for high-salinity environments one of ceramics' most demanding specialties.