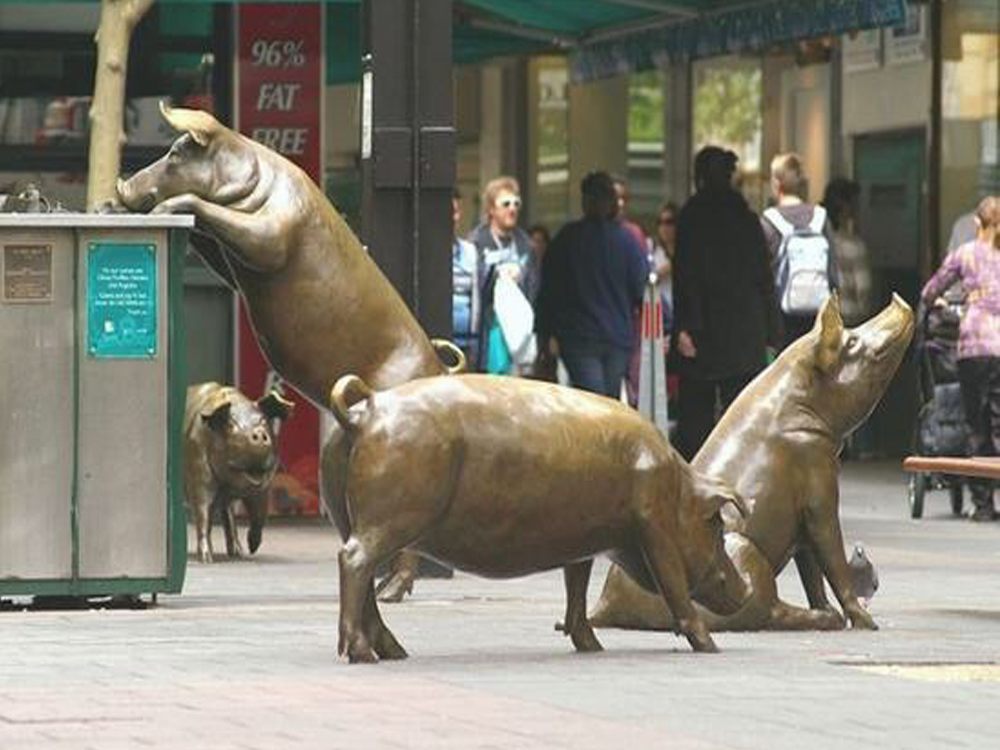
Creating ceramic art requires meticulous attention to detail, especially during the drying and firing stages where cracking and warping can ruin hours of work. Artists employ several proven techniques to avoid these common pitfalls.
1. Slow and Even Drying: Rapid drying is a leading cause of cracks. Artists cover pieces with plastic or damp cloths to control moisture loss, ensuring uniform drying. Larger pieces may be dried in stages to prevent stress fractures.
2. Proper Clay Preparation: Wedging clay thoroughly removes air bubbles that expand during firing, causing cracks. Using the right clay body for the project—whether high-fire or low-fire—also minimizes structural risks.
3. Controlled Kiln Firing: A gradual temperature increase during bisque firing allows moisture to evaporate safely. Artists often use kiln schedules with "soak" periods to stabilize the clay before reaching peak temperatures.
4. Support Structures: For complex shapes, temporary supports or kiln props prevent slumping or warping. Slabs and coils are reinforced to maintain integrity as the clay shrinks.
5. Glaze Application: Uneven glaze layers can create tension during firing. Artists apply coats evenly and test glaze-clay compatibility to avoid thermal shock cracks.
By mastering these methods, artists ensure their ceramics emerge from the kiln intact and visually stunning. Patience and precision are the keys to flawless results.