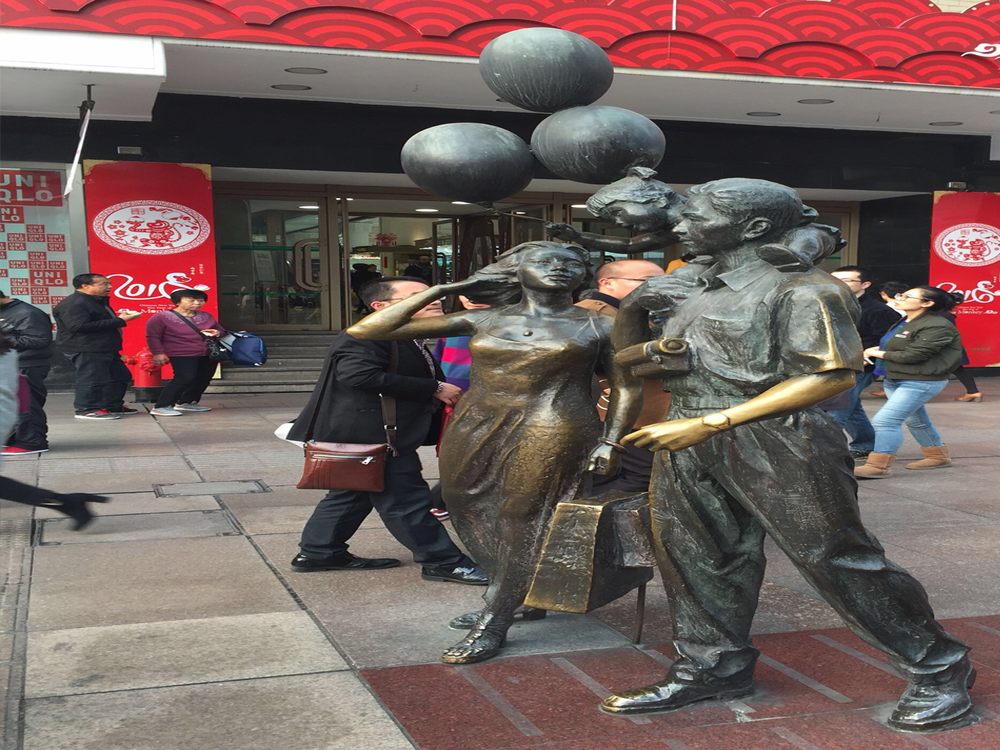
Creating porcelain sculptures with intricate, lace-like details is a testament to an artist's skill, patience, and innovation. To achieve such delicate designs, artists often employ a combination of traditional techniques and modern advancements.
One common method is slip casting, where liquid porcelain (slip) is poured into molds with fine lace patterns. The porcelain hardens, capturing every minute detail. Artists may also use hand-carving tools to refine these details further, ensuring precision.
Another technique involves layering thin sheets of porcelain, which are then meticulously cut or pierced to mimic lace. This requires steady hands and a deep understanding of the material’s behavior during firing, as porcelain shrinks and can warp.
Some artists incorporate 3D printing or laser-cutting technologies to achieve unparalleled intricacy. These tools allow for repetitive patterns and ultra-fine details that would be nearly impossible by hand.
Firing is a critical stage. Porcelain must be fired at high temperatures to achieve its signature translucency and strength. Artists often use multiple firings to preserve delicate structures, applying glazes or underglazes to enhance the lace-like effect.
Ultimately, the fusion of artistry, technical mastery, and innovative tools enables artists to transform fragile porcelain into breathtaking sculptures that resemble delicate lace. Each piece reflects hours of dedication and a profound respect for the medium’s challenges.