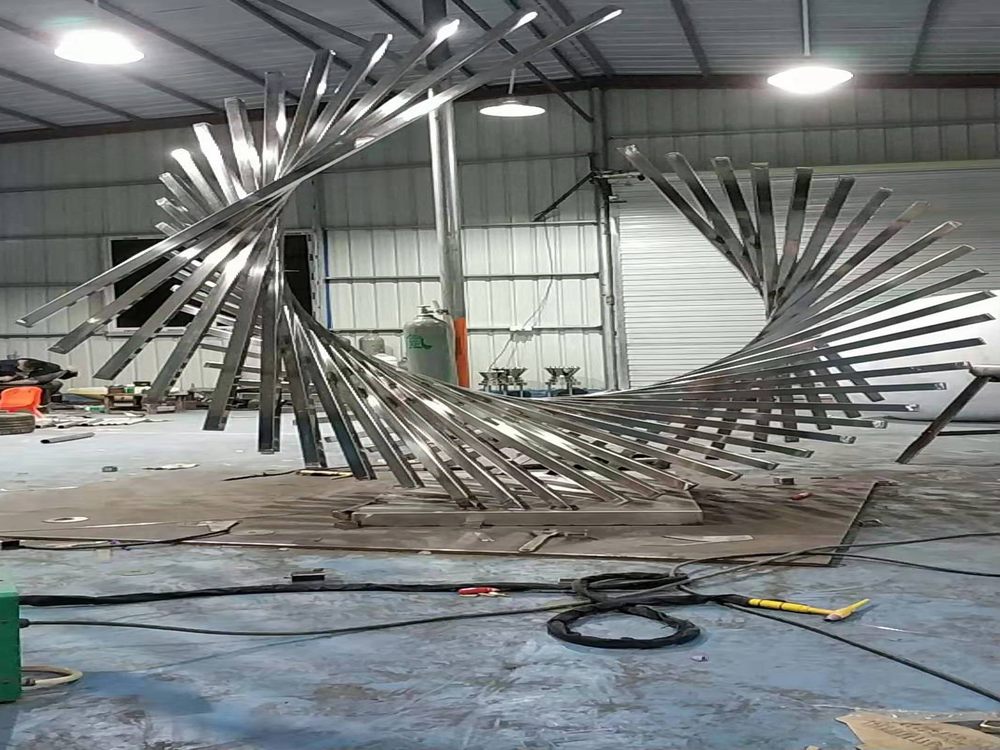
Environmental regulations have significantly transformed the production processes of porcelain sculptures, pushing manufacturers toward more sustainable practices. These regulations primarily affect three key areas: material sourcing, energy consumption, and waste management.
In material sourcing, restrictions on hazardous substances like lead and cadmium have led to the development of safer ceramic glazes. Many studios now use natural mineral pigments and non-toxic binders, which require adjusted firing temperatures and longer curing times.
Energy-intensive kiln operations face strict emissions standards, prompting investments in electric or hybrid kilns. While these reduce carbon footprints, they often demand precise temperature control, adding complexity to the firing process.
Wastewater treatment systems have become mandatory in larger facilities, with clay recycling programs now standard practice. Some artists incorporate regulatory constraints creatively, using recycled porcelain or developing low-fire techniques that conserve energy.
These changes initially increased production costs but ultimately drive innovation in ceramic arts. Many studios now market their compliance as a value proposition, appealing to environmentally conscious collectors. The regulations have also spurred research into alternative materials, potentially revolutionizing porcelain sculpture traditions while preserving artistic integrity.